Category 4 safety light curtain with a protected height of 500mm, watertight housing, multibeam resolution, and 2 fail-safe, OSSD PNP outputs (500mA at 24VDC).
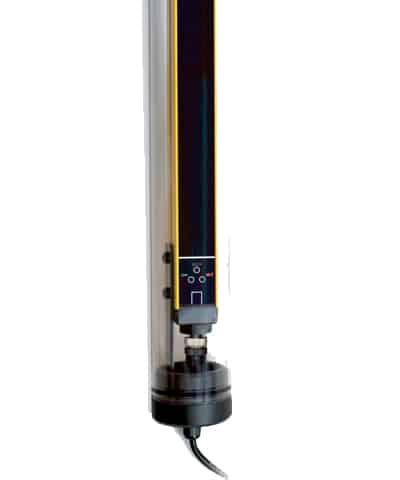
INTERESTED IN A PRODUCT OR SERVICE? Contact Now INTERESTED IN A PRODUCT OR SERVICE? Contact Now INTERESTED IN A PRODUCT OR SERVICE? Contact Now INTERESTED IN A PRODUCT OR SERVICE? Contact Now INTERESTED IN A PRODUCT OR SERVICE? Contact Now INTERESTED IN A PRODUCT OR SERVICE? Contact Now INTERESTED IN A PRODUCT OR SERVICE? Contact Now INTERESTED IN A PRODUCT OR SERVICE? Contact Now INTERESTED IN A PRODUCT OR SERVICE? Contact Now INTERESTED IN A PRODUCT OR SERVICE? Contact Now INTERESTED IN A PRODUCT OR SERVICE? Contact Now INTERESTED IN A PRODUCT OR SERVICE? Contact Now