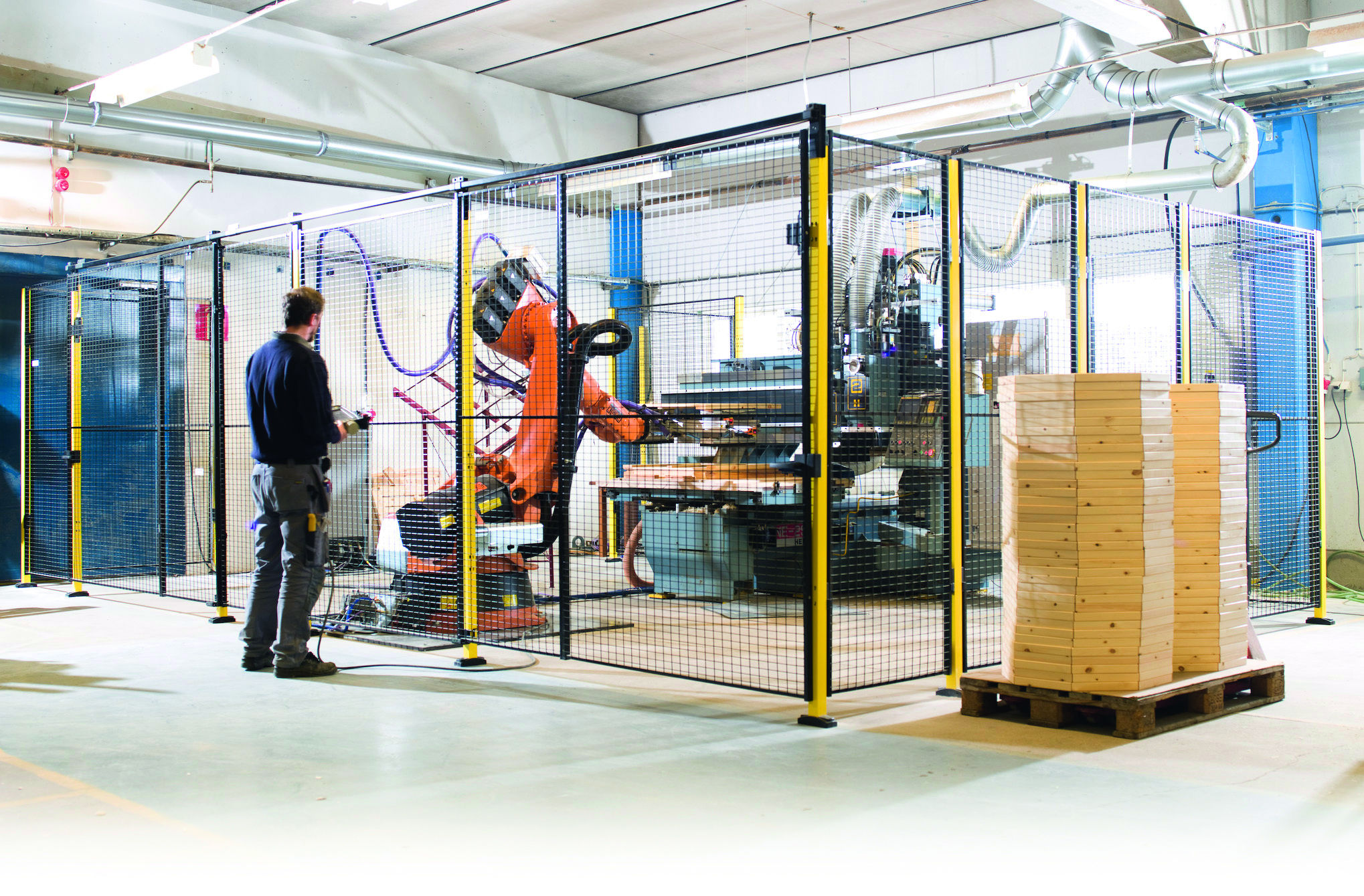
The Ultimate Handbook for Machine and Equipment Safety
The Ultimate Handbook for Machine And Equipment Safety
Nov 29, 2023 | Blog Post, Venus Automation
There are many types of machines used in the Australian Workplace which have potential hazards that can harm workers. The Work Health and Safety Act (2011) has requirements for Person Conduction Business or Undertaking (PCBU) to manage risks associated with the use of a plant. In this short blog we will look into:
- 1. What is machine and equipment safety?
- 2. What are the hazards and risk?
- 3. What products are available?
Recent Posts
What is machine and equipment Safety?
The fundamentals of Machine and equipment safety as per AS 4024.1-2014 involves the practices, protocols, and measures implemented to ensure the well-being of individuals and the protection of property when operating or interacting with various types of machinery and equipment. This involves assessing and mitigating potential hazards, providing proper training for operators, implementing safety features, and adhering to established guidelines and regulations. The goal is to minimize the risk of accidents, injuries, or damage associated with the use of machines and equipment in various industries, ranging from manufacturing and construction to healthcare and beyond.
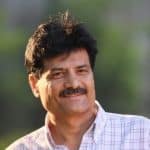
What are the Hazards?
Typical hazards or the dangerous parts of machinery include:
- In running rollers that 'draw you in'
- Shear points
- Flying ejected parts
- Moving parts that can bump and knock
- Hot and cold surfaces
What are risk?
What Safety Products are Avaliable?
A brief overview of the key products that can be integrated into your safety design to ensure your employee’s safety:
Safety Programable Logic Controller (PLC)
Known as a safety PLC, is a specialised type of PLC for the safety automation industry, designed to meet the standard of IEC 62061, ISO 13849-1, and IEC 61058. These devices control and monitor different processes and functions of the machine. Thanks to the nature of PLCs, safety functions can be implemented efficiently and in a customized to the user’s need. With pluggable expansion modules, the safety PLC is also adaptive for larger systems. These PLCs can work in conjunction with various safety sensors and mechanical interlocks.
Find out more by viewing Wieland’s SAMOSPRO range and ReeR’s MOSAIC Series.
Safety Relays
- Safety Relays are devices designed for safety applications meeting the requirements of EN 60947-8-5-1 and EN60204-1. Their primary function is to monitor and manage safety-related processes, acting as a dependable intermediary to execute crucial functions like emergency shutdowns. The relay must met the safety requirement of the circuit having self-monitoring redundancy and must ‘fail-safe’. These devices work in conjunction to safety sensors and interlocks. They are expansion modules available for additional inputs and outputs.
Find out more by viewing our various types of safety relays:
Standalone Safety Relays with 2 N/O Outputs
Standalone Safety Relays with 3 N/O Outputs
Standalone Safety Relays with 4 N/O Outputs
Back EMF Monitoring Relay
Standstill Monitoring and Timer Relays
Time Delay Relays
2 Hand Relays
Expansion Modules
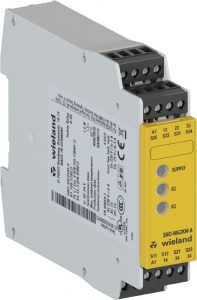
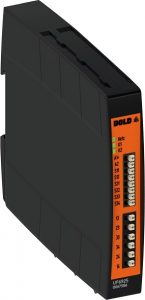
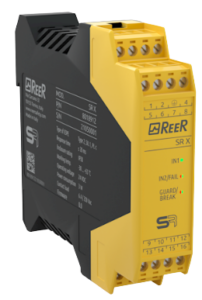
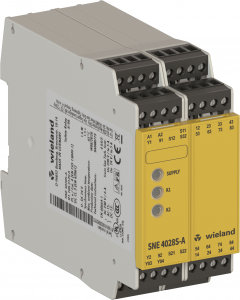
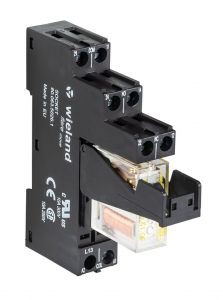
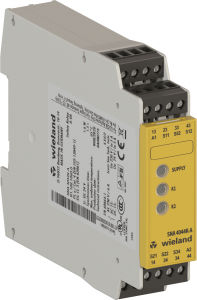
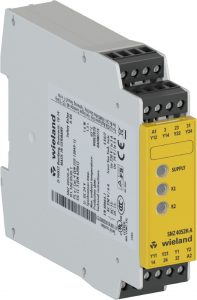
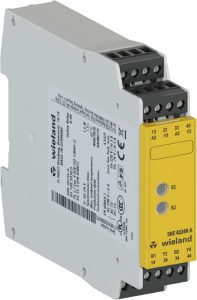
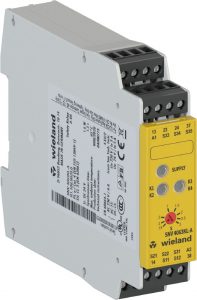
Safety Light CUrtain
Safety Light curtains are a optoelectronic sensor system that uses one or more light beams, emitted by an Emitter and received by a Receiver, to create an array of light breams across an opening or a perimeter. The light curtains will detect the presence or intrusion of objects or people within the defined space, triggering a safety response, such stopping the machine. These devices are made to met the requirement of IEC 61496-1 and IEC 61496-2.
Find out more about our wide range of Light Curtains below:
Non-Contact Safety Sensors
Non-contact safety switches use the principles of RFID, induction, and electromagnetism to determine when to cut power to a machine. These switches have applications in safeguarding machinery, reducing the risk of injuries in hazardous areas.
The advantages of non-contact safety switches include longevity and minimal maintenance requirements make them highly appealing, while their resilience to shock and vibrations ensure reliability in demanding environments. Additionally, the devices can be uniquely coded, making them resistant to tampering and further enhancing their suitability for safety-critical applications. Explore our range of non-contact safety sensors!
Safety Switches and interlocks
Safety switches play a vital role in safeguarding machinery and preventing accidents. Unlike traditional switches, they are designed with a focus on safety, often utilizing features outlined in standards such as ISO 14119:2013. One key advantage of safety switches is their ability to interrupt power or control circuits to machinery, creating a safe state when needed. Safety switches come in different types, including non-contact switches that operate without conductive contacts. They may utilize methods such as magnetic, transponder, or inductor technology to detect when it’s necessary to interrupt power.
Explore our extensive safety switches and interlocks!
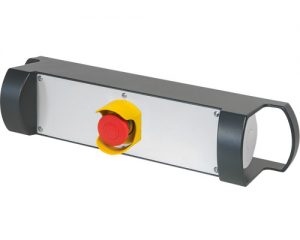
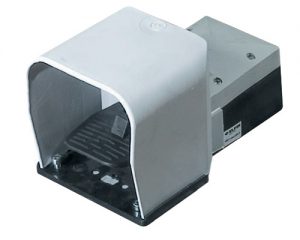
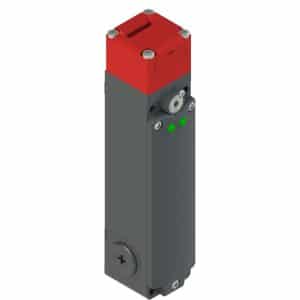
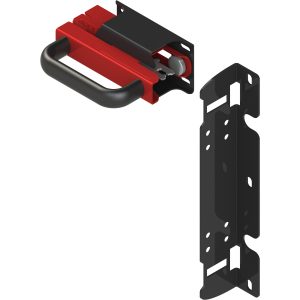
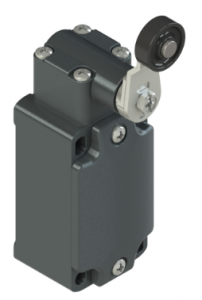
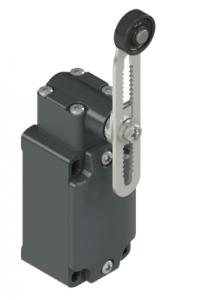
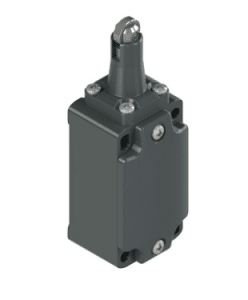
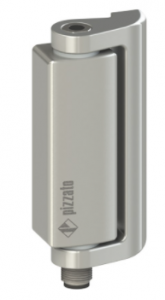
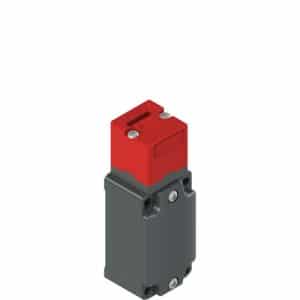
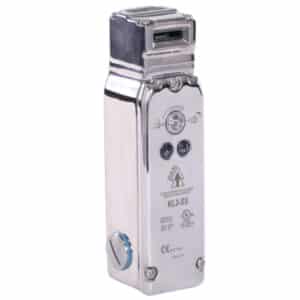

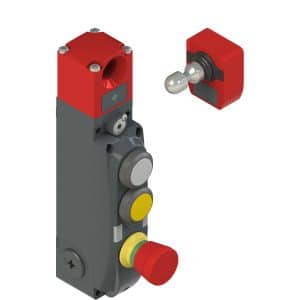
Emergency Stops & Rope Pull switches
Emergency stop (E-stop) switches and rope pull switches are critical components in industrial safety, designed to provide rapid and effective shutdowns in emergency situations.
Emergency Stop (E-stop) Switches: E-stop switches, as the name suggests, are designed for immediate cessation of machinery operation in emergency scenarios. They act as a fail-safe mechanism, cutting power to equipment to prevent accidents or injuries. Adhering to standards like ISO 13850:2015, E-stop switches are strategically placed for quick access, often featuring a distinctive red mushroom-shaped button for easy identification.
Rope Pull Switches: Rope pull switches offer a unique safety solution, particularly in conveyor and material handling systems. In compliance with standards like ISO 13850:2015 and ISO 13856-1:2013, these switches incorporate a pull cord that, when activated, immediately halts machinery. Workers can initiate an emergency stop by pulling the cord from any point along the conveyor, providing a versatile and accessible safety mechanism.
Trapped Key Systems
Trap key systems are sophisticated safety mechanisms employed in industrial settings to control access to hazardous areas and prevent inadvertent equipment activation. These systems typically adhere to standards like ISO 14119:2013, ensuring a systematic and reliable approach to safeguarding machinery.
A trap key system consists of interlocking devices and key exchange units that regulate access to specific zones. These systems are strategically installed in areas where entering or operating machinery poses potential risks. Workers are granted access only when the system ensures a safe state by controlling the removal and exchange of keys.
Many MOre!
We have many more safety products that were not mentioned above! These consist of:
If you need any more assistance contact us on 02 8459 7766 or submit a form: