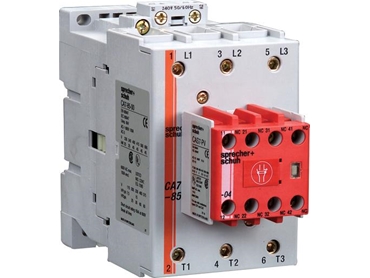
Safety Automation: Safety Contactor Vs Standard Contactor
Safety Automation: Safety Contactor vs. Standard Contactor
Sep 13, 2023 | Blog Post, Venus Automation
In industrial automation, safety takes precedence to protect lives and processes. Understanding the nuances between safety contactors and standard contactors is crucial in ensuring the utmost safety and reliability. In this blog post, we’ll delve into the key distinctions and applications of safety contactors and standard contactors, emphasizing safety automation and design principles.
Understanding Safety Automation
Safety automation forms the foundation of industrial operations, integrating specialized tools such as safety contactors to minimize hazards and safeguard the well-being of employees. Incorporating safety design principles is essential in crafting resilient safety automation systems.
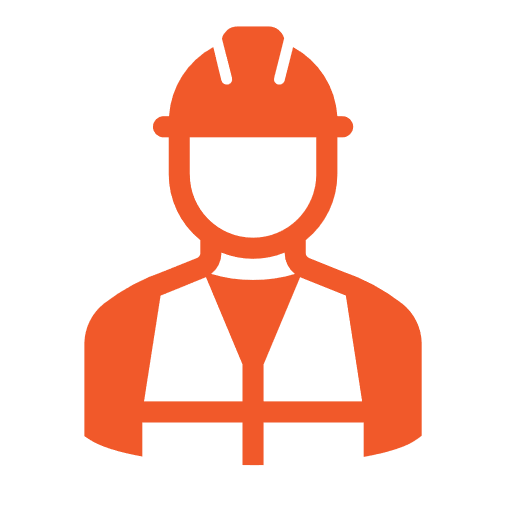
Recent Posts
Standard Contactors: Versatile, Yet Not for Safety Automation
1. Purpose and Function:
Standard contactors serve many applications but are not tailored for safety automation. They excel in controlling electrical circuits across industries but lack the specialized safety features found in safety contactors.
2. Mechanical Linked Contacts:
Standard contactors may or may not have mechanically linked contacts, making them less suitable for safety-critical applications.
3. Manual Operation Prevention:
Normal contactors often allow manual operation from the front of the device, which is convenient for standard control tasks but poses safety risks in critical scenarios.
4. Auxiliary Contacts:
Auxiliary contacts in standard contactors may have a different level of secure fixing, increasing susceptibility to detachment.
Safety Contactors: The Guardians of Safety Automation
1. Purpose and Function:
Safety contactors are purpose-built for safety automation, where lives and processes hang in the balance. Their primary function is to enable rapid and secure shutdown or isolation of machinery and procedures during emergencies.
2. Mechanical Linked Contacts:
A hallmark feature of safety contactors is their mechanically linked contacts. These contacts act as a cohesive unit, closing or opening in unison to ensure a fail-safe open state in case of a failure. This critical safety feature aligns with stringent safety design principles.
3. Manual Operation Prevention:
Safety contactors are engineered to prevent manual operation from the front of the device, reducing the risk of accidental actions that could trigger unsafe conditions. This aligns with safety design principles aiming to prevent unexpected start-ups.
4. Securely Fixed Auxiliary Contacts:
Auxiliary contacts in safety contactors are securely affixed to the device, deterring detachment due to environmental factors or tampering. This enhances the overall reliability of safety automation systems.
5. Reliability Data:
Safety contactors provide reliability data, typically in the form of a B10d value. This data is indispensable for evaluating the reliability of safety automation systems, adhering to safety design principles.
6. Positively Driven Contacts (EN 60947-5-1, Annex L):
Definition: Positively driven contact elements in accordance with EN 60947-5-1, Annex L, are a combination of n NO contacts and NC contacts whose construction prevents their simultaneous closing.
Application: These contact elements are primarily used in contactor relays.
Verification Tests: Tests are defined to verify the positively driven contactor relay contacts’ characteristics.
Characteristics: These characteristics ensure that NO and NC contacts in a contactor relay cannot close at the same time, which is crucial in applications where safety or proper sequence of operations is critical.
7. Mirror Contacts (EN 60947-4-1, Annex F):
Definition: A mirror contact in accordance with EN 60947-4-1, Annex F, is an auxiliary NC contact which cannot be closed simultaneously with an NO main contact.
Application: These mirror contacts are primarily used in power contactors.
Verification Tests: Tests are defined to verify the mirror contact characteristics.
Characteristics: Mirror contacts ensure that the NC auxiliary contacts do not close when the NO main contacts are closed, which can be essential in power control applications.
Choosing the Right Contactor for Your Safety Design:
Selecting between safety contactors and standard contactors hinges on your application’s nature:
Safety Contactors: These are indispensable in safety automation when safeguarding lives and critical processes is paramount. They are integral to environments where human well-being and process integrity are at risk.
Standard Contactors: Ideal for general control tasks, standard contactors are versatile and dependable in standard industrial and commercial settings.
In conclusion, safety automation and design principles are the bedrock of industrial processes. Safety contactors, purpose-built for safety automation, are pivotal in ensuring worker safety and process reliability. While dependable for general applications, standard contactors lack the specialized safety features necessary for safety automation.