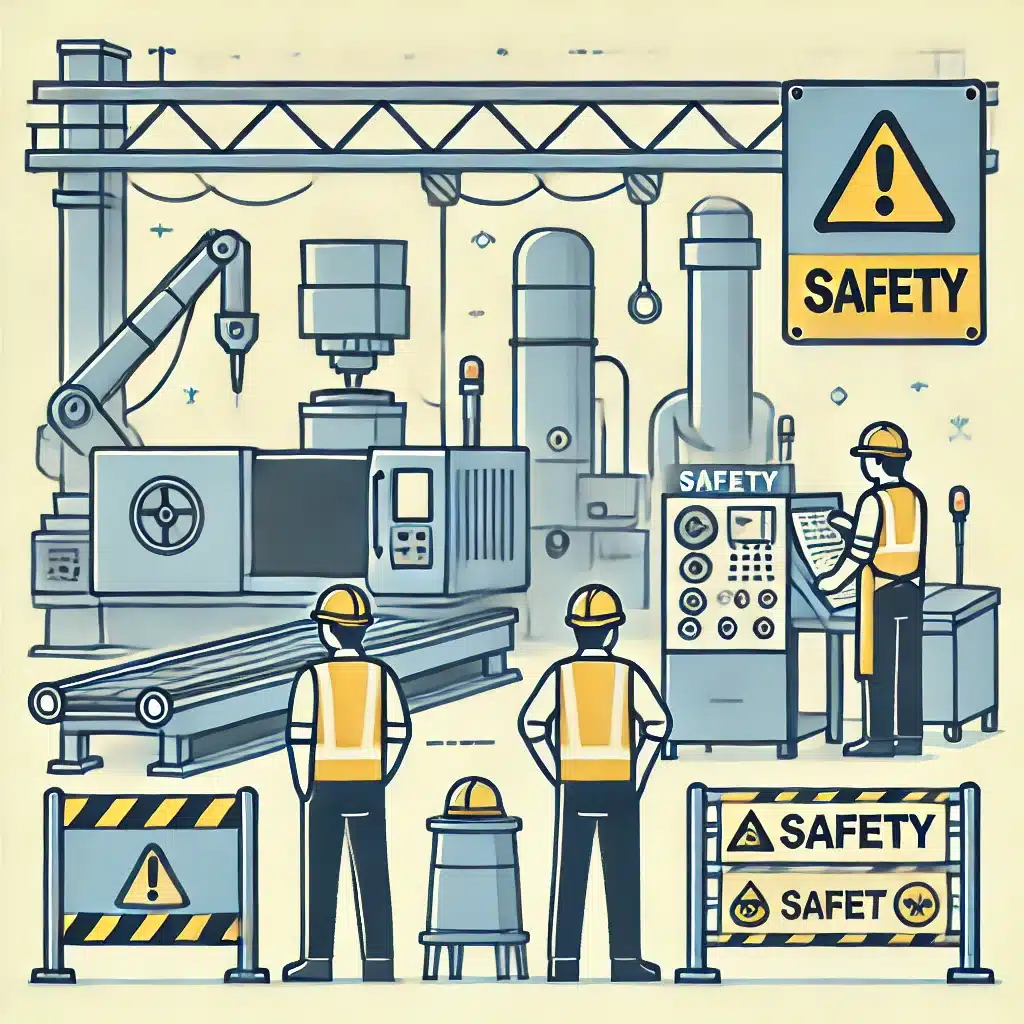
Boost Workplace Safety with Non-Contact Sensors & Locks
An brief overview of safety sensors & switches
January.10 2024 | Blog Post, Venus Automation
In today’s industrial settings, ensuring workplace safety is paramount. Safety sensors and switches provide intelligent, reliable solutions to protect workers and equipment. These devices are fundamental in preventing accidents, enhancing operational efficiency, and maintaining compliance with safety standards, making them indispensable in modern workplace protection systems.
Safety Sensors: Precision in Hazard Detection
Safety sensors are designed to detect and mitigate risks before they escalate, enabling a proactive approach to workplace safety. Inductive proximity sensors, for example, monitor the presence of metallic objects near machinery, ensuring smooth and hazard-free operations. These sensors eliminate physical contact, reducing wear and prolonging the lifespan of critical equipment.
For applications requiring advanced security, RFID Safety & Magnetic Switch provide dynamic monitoring of guard positions. These sensors ensure protective barriers are properly engaged and immediately alert operators to unauthorized access or unsafe conditions. Additionally, stainless-steel safety sensors are tailored for environments with extreme conditions, such as exposure to moisture, chemicals, or high temperatures, delivering consistent performance across a wide range of industries. Magnetic coded sensors add another layer of versatility, particularly in areas where precise positioning and alignment of machine guards are critical. These sensors operate without physical contact and can detect whether guards or doors are fully closed, helping to prevent inadvertent access to dangerous zones. Their robust design ensures reliability in demanding industrial environments.
Safety Switches: Reliable Access Control and Emergency Stops
Safety switches complement sensors by providing physical control over access points and machinery. They are critical for securing hazardous areas and ensuring that operations are conducted only when conditions are safe.
Interlock safety switches are commonly used to lock guards or enclosures during machine operations. These switches prevent accidental access to dangerous areas until it is safe to proceed, safeguarding both workers and equipment. In emergencies, emergency stop switches offer a rapid and reliable method to halt operations, minimizing the risk of injuries or damage.
These devices are built to withstand demanding industrial environments, offering durability and tamper-proof functionality. Their reliability underpins their role as a cornerstone of workplace safety systems.
Recent Posts
Drive safety and efficiency forward - safety sensors & switch
Safety sensors and switches are more than just safety tools—they are enablers of smarter, more efficient industrial environments. These technologies provide real-time hazard monitoring and precise control over critical processes, ensuring a seamless balance between productivity and safety.
Safety sensors, such as inductive proximity or RFID devices, detect potential risks before they escalate, minimizing equipment damage and operational disruptions. Their ability to work in challenging conditions, like extreme temperatures or chemical exposure, further enhances reliability. Safety switches, including emergency stop and interlock mechanisms, ensure quick responses and prevent unauthorized access to hazardous zones, safeguarding personnel and machinery.
Beyond immediate safety, these tools contribute to long-term operational resilience. By reducing accident-related downtime and maintenance needs, they improve resource allocation and operational flow. Integrating safety sensors and switches into workplace systems demonstrates a commitment to innovation, compliance, and the well-being of employees, paving the way for sustainable industrial success.
Inductive Proximity Sensors for Workplace Safety
Inductive proximity sensors are vital components in modern industrial safety systems, offering unmatched precision and reliability in detecting metallic objects without physical contact. These sensors operate by generating an electromagnetic field that reacts to metal within its range, providing swift detection and accurate responses to potential hazards. By triggering alerts or shutdowns when metallic items encroach on hazardous zones, they prevent accidents, protect equipment, and enhance operational safety.
Their robust, non-contact design ensures minimal wear and extends the lifespan of both the sensors and the machinery they monitor. This durability makes them particularly effective in harsh industrial environments where factors like dust, oil, vibration, or extreme temperatures can challenge traditional safety devices. Furthermore, their ability to prevent misalignment or obstructions in equipment reduces downtime and maintenance costs.
Applications Across Industries: Inductive proximity sensors are indispensable in various industries, from manufacturing to logistics. In assembly lines, they verify the presence or absence of metallic components, ensuring flawless assembly processes and preventing costly malfunctions. In automated systems, they maintain alignment of moving parts and detect potential obstructions to avoid collisions and operational disruptions. For conveyor systems, these sensors ensure precise position sensing, enabling smooth transitions and efficient material handling.
Additionally, inductive proximity sensors play a critical role in safety mechanisms, such as automatically halting machinery when unauthorized metallic objects enter restricted areas. Their integration into workplace safety systems not only enhances hazard detection but also supports automation, improving both safety and productivity.These sensors are not just safety tools—they are essential components in creating a resilient, future-ready workplace.
our featured products
Enhanced Safety with Magnetic-Coded Sensors
Magnetic-coded sensors are transformative devices in workplace safety, delivering advanced solutions for access control and hazard prevention. Utilizing unique magnetic codes, these sensors ensure that safety doors and guards are properly secured before machinery operates, preventing accidents caused by misalignment or unauthorized access.
Unlike traditional safety mechanisms, magnetic-coded sensors prioritize precision and adaptability, making them highly suitable for dynamic industrial environments. Their application extends across industries, such as manufacturing, logistics, and pharmaceuticals, where safeguarding automated systems is critical. These sensors excel in monitoring complex machinery, ensuring that processes remain secure and aligned with safety protocols.
Beyond safety, magnetic-coded sensors contribute to a proactive safety culture by integrating with automation systems for real-time monitoring and emergency responses. They empower industries to meet regulatory compliance while maintaining productivity, reinforcing their role as a vital component of workplace protection strategies.
our featured products
RFID switch - industry safety
As industries continue to prioritize worker safety and operational efficiency, advanced technologies like RFID safety switches and magnetic switches are redefining workplace protection. These devices serve as critical components in modern safety systems, offering precise control, real-time monitoring, and secure access management in industrial settings.
RFID safety switches use radio-frequency identification to verify the correct positioning of guards, doors, and enclosures. Unlike traditional mechanical solutions, they operate contactless devices, ensuring seamless integration into automated systems. Their ability to detect tampering and provide unique coding for each application enhances security while preventing unauthorized access or manipulation. This makes RFID safety switches an ideal choice for applications requiring traceability and advanced monitoring, such as pharmaceutical manufacturing, robotics, and food processing.
Magnetic safety switches, on the other hand, provide a robust solution for environments with extreme conditions like high humidity, vibration, or dust. These switches utilize magnetic fields to detect proper alignment and ensure equipment operates only under safe conditions. Their versatility and simplicity make them indispensable in conveyor systems, assembly lines, and hazardous areas requiring fail-safe mechanisms.
By incorporating RFID and magnetic switches, industries can achieve unparalleled safety and compliance, empowering businesses to protect their workforce while driving productivity in increasingly complex operations. These technologies are not just innovations—they are essential tools for a safer future.
Our featured products
Stainless-Steel Safety Devices for Workplace Protection
In industries where safety and hygiene are non-negotiable, stainless-steel electronic safety devices have become indispensable. These devices are engineered to meet the demands of environments where moisture, chemicals, and extreme temperatures are everyday challenges. Beyond their robust design, they integrate advanced safety monitoring capabilities to secure machinery and prevent accidents.
A key advantage of stainless-steel safety devices is their ability to operate reliably in washdown areas, ensuring compliance with hygiene regulations in sectors like food processing and pharmaceuticals. Unlike traditional materials, stainless steel resists corrosion and bacterial growth, making it ideal for maintaining both equipment longevity and cleanliness.
These devices are not just about physical durability; they are integral to intelligent safety systems. By monitoring access points and enforcing controlled operations, they prevent unauthorized access and reduce the risk of contamination. In chemical industries, for instance, they play a vital role in maintaining containment and protecting workers from hazardous substances.
Stainless-steel safety devices go beyond safeguarding operations—they contribute to a culture of accountability and precision. By enhancing operational efficiency, ensuring compliance, and prioritizing employee well-being, they exemplify how technology can transform workplace safety into a cornerstone of industrial success.
The strength of stain-steel safety products comparing to another material
Stainless-steel safety devices offer unique strengths that set them apart from other safety solutions. Their seamless integration into demanding industries is unmatched due to their ability to endure intense cleaning protocols and high-impact environments. Unlike other materials, stainless steel maintains structural integrity under extreme mechanical stress, ensuring consistent performance over time.
These devices are specifically engineered to thrive in corrosive atmospheres, such as chemical manufacturing or salt-rich environments, where other safety products might degrade. Their aesthetic appeal also makes them suitable for industries like pharmaceuticals, where cleanroom compliance and visual clarity are crucial.
Furthermore, stainless-steel devices support versatile configurations, allowing for customization to meet specific operational challenges. They effectively bridge the gap between robust protection and aesthetic requirements, enhancing safety without compromising design or usability. By offering unparalleled adaptability and reliability, stainless-steel safety devices redefine workplace safety standards for industries with unique and rigorous demands.
our featured products
The overview of Solenoid Locking Switches.
Solenoid locking switches are essential safety devices designed to control access to hazardous machinery and ensure that operators cannot enter dangerous zones during unsafe conditions. These switches use an electromechanical mechanism that locks or releases access points based on control signals, adding a critical layer of protection in industrial environments.
The solenoid mechanism functions by generating a magnetic force that activates the lock. When a machine is operating or presents a risk, the solenoid engages to lock safety doors, covers, or gates, preventing unauthorized access. The system releases the lock only when the machine has completed its operation or when it is deemed safe to access. This ensures that operators can only enter the restricted area during safe conditions, significantly reducing the risk of accidents.
Solenoid locking switches are available in two configurations: power-to-lock and power-to-release. In power-to-lock systems, the solenoid engages when power is supplied, keeping the door locked until power is cut. This configuration is ideal for critical safety zones, as it maintains the lock even during power failures. In contrast, power-to-release systems unlock when power is supplied, often used for emergency access scenarios where quick entry is required.
In out product range, there are divided in two types. Electro-magnetic switches use magnetic force to lock safety doors, while tongue solenoid switches use a mechanical tongue actuator for secure interlocking, ensuring controlled access during hazardous machine operations. These switches are widely used in industries such as manufacturing, food processing, packaging, and robotics, where high-speed machinery and automated systems present potential hazards. Their robust design ensures reliable performance in harsh environments, including exposure to dust, moisture, and extreme temperatures.
By implementing solenoid locking switches, businesses can enhance worker protection, ensure compliance with safety regulations, and prevent costly accidents. These switches not only safeguard employees but also improve productivity by minimizing downtime and ensuring that processes are halted only when absolutely necessary. This makes solenoid locking switches an indispensable component in modern industrial safety systems.
understand workers' safety awareness -
Get locking switches on.
Worker awareness is a cornerstone of workplace safety and efficiency, particularly in industries where interactions with high-risk machinery are routine. Solenoid locking switches are not just technical solutions—they are tools for fostering a culture of mindfulness, responsibility, and proactive safety among employees.
These devices function by locking safety doors and guards until hazardous operations are fully halted, preventing premature access to machinery. However, their significance extends beyond their mechanical function. Solenoid locking switches serve as constant visual and functional reminders of safety protocols, requiring workers to pause, assess, and engage consciously with their tasks. This moment of interaction reinforces an essential awareness: that safety is a shared responsibility, not merely the result of automated systems.
The procedural discipline required by solenoid locking switches nurtures a deeper understanding among workers about the consequences of bypassing safety measures. Employees become more attuned to the importance of verifying operational statuses, properly securing equipment, and adhering to protocols. This heightened awareness minimizes complacency, encourages active participation in safety measures, and reduces human errors that often lead to accidents.
By integrating solenoid locking switches, organizations empower workers to internalize safety as an active mindset rather than a passive obligation. This shift transforms workplace dynamics, fostering not just compliance but a culture of safety ownership and collective well-being.
Role of electro - magnetic locking switches in workplace
Electro-magnetic locking switches are essential for safeguarding industrial operations by providing secure, controlled access to hazardous areas. These switches utilize magnetic force to lock safety doors, ensuring that machinery operates only when access points are securely closed. This eliminates the risk of unauthorized entry and accidental exposure to moving parts, significantly reducing workplace accidents.
Unlike traditional mechanical locks, electro-magnetic locking switches feature a non-contact mechanism that minimizes wear and ensures long-term reliability. This makes them particularly suited for high-demand environments, such as automated assembly lines, robotic workstations, and high-speed packaging systems, where consistent performance is critical.
These switches are not just about securing doors—they integrate seamlessly into safety systems to provide intelligent control. For instance, they can lock access points during active operations and release them only when machinery has completely stopped or safety conditions are met. This advanced functionality supports compliance with stringent safety standards and ensures that hazardous processes are effectively contained.
Electro-magnetic locking switches are a cornerstone of industrial safety, offering robust protection, reducing maintenance needs, and supporting operational efficiency. Their ability to combine durability with precision makes them indispensable in environments where safety, reliability, and compliance are paramount.
Our featured products
the safework enhanced by tongue locking switch.
In industrial environments where heavy machinery and hazardous operations are routine, tongue solenoid interlock switches are indispensable for maintaining safety and operational integrity. These switches provide a sophisticated locking mechanism designed to control access to high-risk areas, ensuring that safety doors and guards remain locked until machinery has completely stopped.
The unique tongue-shaped actuator integrates seamlessly with interlocking systems, offering more than mechanical security. It acts as a vital checkpoint, ensuring workers cannot enter hazardous zones prematurely. This controlled access prevents accidental exposure to moving parts and eliminates the risk of unintended restarts, significantly reducing workplace injuries.
What sets tongue solenoid interlock switches apart is their integration into advanced safety protocols. These devices not only secure physical barriers but also communicate with automated systems to confirm safe conditions before granting access. This functionality aligns with modern safety standards, providing industries with a comprehensive solution for managing complex machinery operations.
Moreover, their robust design ensures reliable performance even in harsh environments, making them suitable for demanding industries like automotive manufacturing, food processing, and robotics. By prioritizing controlled access, minimizing human error, and ensuring compliance with safety regulations, tongue solenoid interlock switches represent a cornerstone of industrial safety, protecting both workers and operations.
Our featured products
Conclusion
Safety non-contact sensors and solenoid locking switches play a critical role in ensuring workplace safety by controlling access points, monitoring hazardous zones, and preventing machinery from operating under unsafe conditions. Non-contact sensors enhance safety by detecting proximity or motion without physical contact, reducing wear and tear on equipment and minimizing downtime. Their ability to trigger automated shutdowns during unsafe situations significantly reduces the risk of accidents.
Solenoid locking switches add another layer of security by physically locking access doors and gates until it is safe to enter restricted areas. Using an electromechanical mechanism, these switches prevent unauthorized access and ensure machinery remains immobilized until all hazards are neutralized. Unlike basic interlocks, solenoid switches resist unauthorized overrides, reinforcing compliance with strict safety protocols.
Together, these devices strengthen workplace safety systems, helping businesses comply with safety regulations and protect employees from life-threatening incidents. By integrating both technologies, organizations can improve operational efficiency, reduce risks, and demonstrate a commitment to employee well-being. This comprehensive safety approach not only safeguards personnel but also minimizes downtime, enhancing productivity while fostering a culture of safety.