Explore the ReeR CJ30 Female Connector Cable, 30m M23 19-pole straight connector, 24V DC power supply, designed for industrial automation applications.
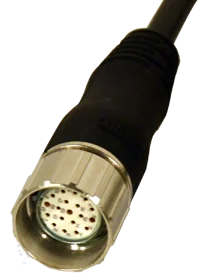
INTERESTED IN A PRODUCT OR SERVICE? Contact Now INTERESTED IN A PRODUCT OR SERVICE? Contact Now INTERESTED IN A PRODUCT OR SERVICE? Contact Now INTERESTED IN A PRODUCT OR SERVICE? Contact Now INTERESTED IN A PRODUCT OR SERVICE? Contact Now INTERESTED IN A PRODUCT OR SERVICE? Contact Now INTERESTED IN A PRODUCT OR SERVICE? Contact Now INTERESTED IN A PRODUCT OR SERVICE? Contact Now INTERESTED IN A PRODUCT OR SERVICE? Contact Now INTERESTED IN A PRODUCT OR SERVICE? Contact Now INTERESTED IN A PRODUCT OR SERVICE? Contact Now INTERESTED IN A PRODUCT OR SERVICE? Contact Now