The Pizzato CS MF204M0-P10 module offers SIL 3, PL e compliance, ensuring high-performance safety monitoring of guard and emergency stop functions.
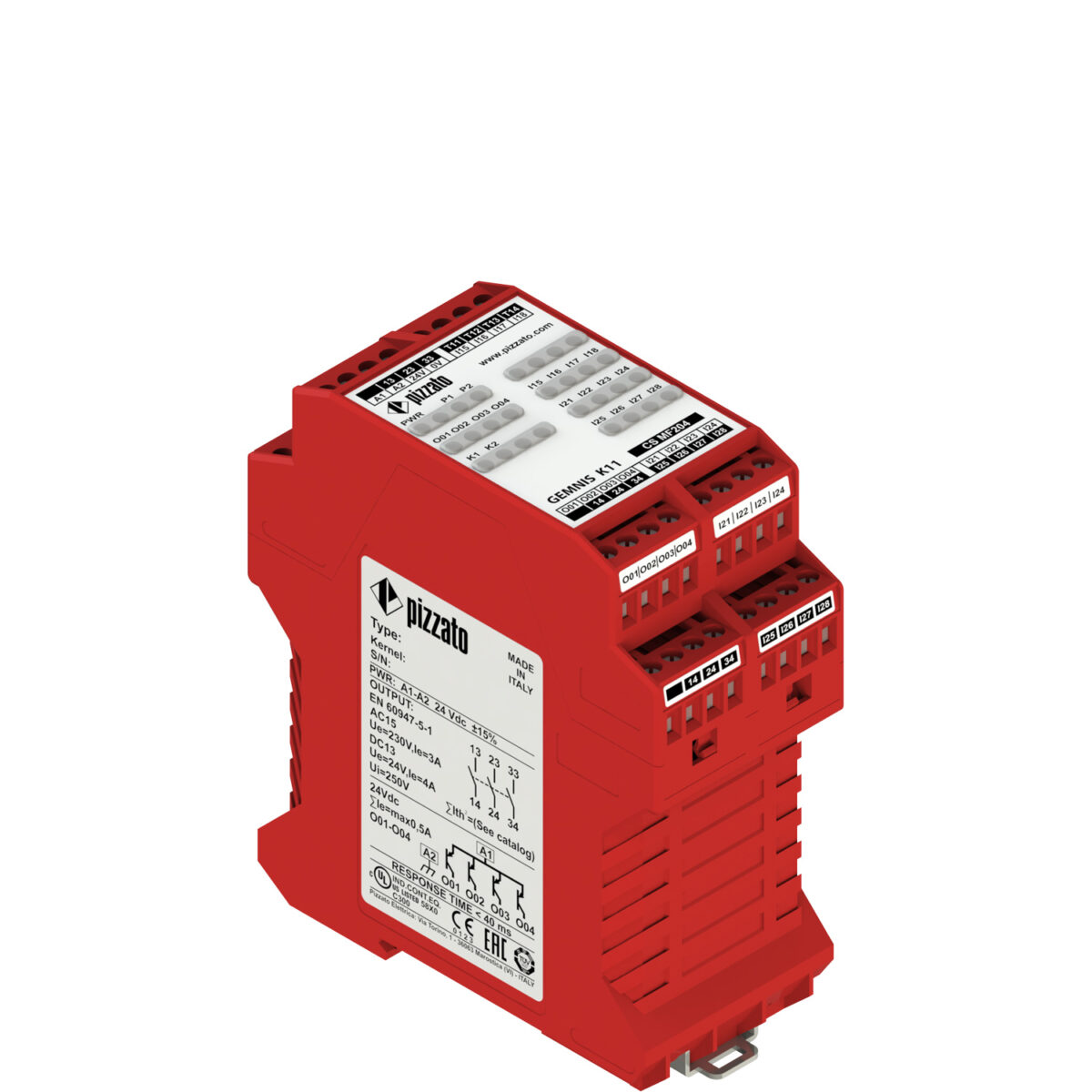
INTERESTED IN A PRODUCT OR SERVICE? Contact Now INTERESTED IN A PRODUCT OR SERVICE? Contact Now INTERESTED IN A PRODUCT OR SERVICE? Contact Now INTERESTED IN A PRODUCT OR SERVICE? Contact Now INTERESTED IN A PRODUCT OR SERVICE? Contact Now INTERESTED IN A PRODUCT OR SERVICE? Contact Now INTERESTED IN A PRODUCT OR SERVICE? Contact Now INTERESTED IN A PRODUCT OR SERVICE? Contact Now INTERESTED IN A PRODUCT OR SERVICE? Contact Now INTERESTED IN A PRODUCT OR SERVICE? Contact Now INTERESTED IN A PRODUCT OR SERVICE? Contact Now INTERESTED IN A PRODUCT OR SERVICE? Contact Now