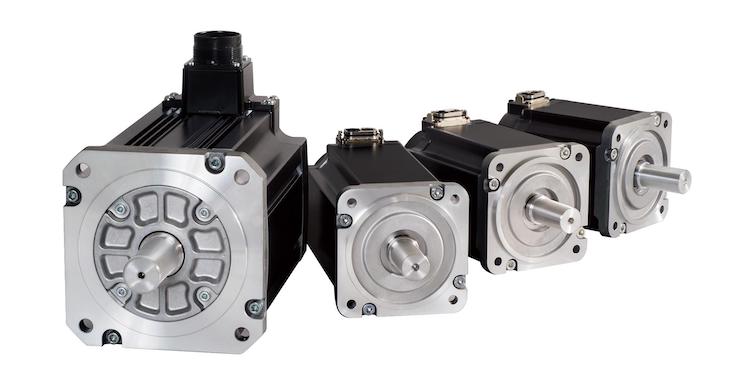
2
How to Choose the Right Servo Motor
Definition and Functionality
Servo motors are high-performance actuators used to precisely control the angular or linear position, velocity, and acceleration of mechanical components. Commonly found in industrial automation, robotics, and CNC machinery, these motors rely on feedback mechanisms—typically from encoders or potentiometers—to maintain accurate motion control.
A typical servo system includes a motor, a controller, and a sensor. The controller sends a command signal, the motor responds with movement, and the sensor provides feedback to ensure the motor reaches and maintains the desired position. This closed-loop system allows servo motors to achieve exceptional precision, which is critical in applications like automated assembly lines, robotic arms, or even camera stabilization systems.
Servo motors are widely used in industrial automation for their reliability, compact design, and ability to deliver consistent torque across a wide speed range. Whether in packaging machines or conveyor systems, their functionality ensures efficient and accurate motion control in demanding environments.
Types of Servo Motors
These are widely used in industrial applications due to their high efficiency and robust torque capabilities. AC servo motors are ideal for high-speed, high-power tasks, such as in automated manufacturing and CNC machining.
Known for their simplicity and ease of control, DC servo motors are commonly used in smaller-scale applications like hobby robotics, actuators, and educational kits.
These motors eliminate the mechanical brushes found in traditional designs, offering longer life, lower maintenance, and higher efficiency. Brushless designs are popular in high-end robotics and precision medical equipment.
Unlike rotary types, linear servo motors produce direct linear motion without needing additional mechanical conversion. They are favoured in systems that demand ultra-precise positioning, such as semiconductor manufacturing.
Evaluate Application Load Requirements
Torque Needs Assessment
Understanding the torque requirements of your application is essential when selecting the right servo motor for industrial automation systems. Torque refers to the rotational force the motor must generate to move a load efficiently and accurately. Undersized torque can lead to poor performance, overheating, or mechanical failure, while an oversized motor increases cost and energy consumption unnecessarily.
To assess torque needs accurately, consider the total load weight, friction, inertia, and any external forces acting on the system. For instance, in a packaging line where products are moved quickly and repeatedly, the servo motor must generate consistent torque to maintain precise motion control despite variations in load size or speed. Tools like torque-speed curves and load simulation software can help match a servo motor’s output to your system’s requirements. Factoring in both continuous and peak torque demands ensures long-term reliability and minimizes wear during high-load cycles.
Speed Capabilities Determination
Alongside torque, evaluating the speed capabilities of a servo motor is critical to meeting your application’s performance goals. Speed, typically measured in revolutions per minute (RPM), dictates how fast a motor can complete a task. In motion control systems, this directly affects cycle time, throughput, and overall efficiency.
Start by identifying the operational speed your application requires—whether it’s a slow and steady motion in a robotic joint or rapid acceleration in a pick-and-place system. It’s important to consider both maximum and sustained speeds to avoid motor stress or control lag.
Modern servo motors designed for industrial automation can maintain high speeds without compromising accuracy, especially when paired with the right feedback device. Matching speed capabilities to your system’s load and duty cycle ensures responsive, smooth motion under all operating conditions.
Consider Power Supply Compatibility
Voltage and Current Requirements
When selecting a servo motor for any motion control system, ensuring compatibility with your power supply is a crucial step. Servo motors operate within specific voltage and current ranges, and mismatched values can lead to underperformance, overheating, or complete system failure.
Start by reviewing the rated voltage of the servo motor and ensure it aligns with your available power source—whether it’s a low-voltage 24V DC system or a high-voltage 400V AC industrial setup. Beyond voltage, current requirements must be carefully assessed, especially during motor startup and peak load conditions. A motor drawing more current than your power supply can provide may cause protective shutdowns or electrical damage.
In industrial automation settings, where multiple axes or high-speed motion is involved, using regulated power supplies with sufficient headroom is essential for maintaining reliable performance across all servo drives.
Control System Integration
Integrating your servo motor with the broader control system—such as a PLC or motion controller—requires careful attention to communication protocols, signal compatibility, and I/O requirements. A servo motor may support interfaces like analog signals, pulse/direction inputs, or digital fieldbus protocols such as EtherCAT, CANopen, or Modbus. Choosing a servo motor that can seamlessly integrate with your existing control architecture reduces setup time and ensures stable performance. For example, a servo drive that supports real-time feedback via Ethernet-based communication can improve precision and synchronization in complex automation lines.
Additionally, ensure the servo motor’s encoder or feedback device is compatible with your controller’s input requirements. This alignment allows for accurate position and speed control—critical for tasks like coordinated multi-axis motion or high-speed sorting systems.
Assess Environmental Conditions
Temperature and Humidity Considerations
Environmental conditions play a significant role in determining the performance and longevity of servo motors in industrial automation. Operating a motor outside its specified temperature or humidity range can lead to degraded efficiency, insulation breakdown, or premature failure.
Most standard servo motors are rated for environments between 0°C and 40°C. However, applications in food processing, outdoor machinery, or high-heat manufacturing may require models with extended temperature ratings or integrated cooling features. In high-humidity environments, condensation can cause corrosion or short circuits. Choosing a servo motor with proper sealing and moisture-resistant materials helps ensure reliable operation under these conditions. For critical applications, it’s also important to consider thermal management—ensuring sufficient airflow or heat dissipation to maintain optimal performance during continuous duty cycles.
Resistance to Dust and Chemicals
In harsh industrial environments, servo motors are often exposed to airborne dust, oil mist, or chemical vapors that can compromise mechanical and electrical components. To address these challenges, many servo motors are designed with ingress protection (IP) ratings that indicate their ability to resist solid particles and moisture. For instance, a motor with an IP65 rating is well-suited for dusty factory floors or areas with occasional water spray. In sectors like chemical processing or metal fabrication, where corrosive agents are present, using servo motors with chemically resistant coatings or stainless-steel housings can significantly extend service life. Selecting a servo motor built for your specific environmental conditions ensures consistent motion control performance and reduces downtime caused by environmental wear and tear.
Choose the Appropriate Feedback System
Encoders vs. Resolvers
Servo motors rely on feedback devices to monitor position, speed, and direction, enabling accurate motion control in industrial automation systems. The two most common feedback technologies—encoders and resolvers—offer different advantages depending on the application. Encoders provide digital feedback, delivering high-resolution position data that allows for precise control. They are available in incremental and absolute types, with absolute encoders offering a unique position value even after power loss. Encoders are ideal for applications that demand tight accuracy, such as semiconductor manufacturing or robotics, where even small deviations can impact performance.
Resolvers, on the other hand, are analog devices known for their durability and resistance to harsh conditions like high temperatures, vibration, and electrical noise. While they offer lower resolution than encoders, resolvers are often used in environments such as heavy machinery or military-grade equipment where reliability outweighs ultra-precise feedback. Choosing between an encoder and a resolver depends on the balance between environmental demands, required precision, and system complexity.
Importance of Precise Control
Precise control is at the heart of any servo motor application, especially in industries where accuracy translates directly to product quality and operational efficiency. Feedback systems play a key role in enabling this precision by continuously relaying real-time position and speed data back to the controller.
In high-performance motion control systems—such as CNC machining, automated pick-and-place robots, or coordinated multi-axis systems—precision feedback ensures smooth transitions, exact positioning, and minimized error margins. Without it, servo motors risk overshooting, instability, or inconsistent performance, all of which can compromise output.
A well-matched feedback system not only improves accuracy but also enhances system responsiveness and fault detection, supporting predictive maintenance and long-term reliability. For industrial automation setups that demand both speed and accuracy, investing in the right feedback technology is essential.
Evaluate Mechanical Design Constraints
Motor Size and Weight
When integrating servo motors into a motion control system, size and weight play a critical role—especially in compact or mobile applications. A motor that’s too large can complicate installation, interfere with adjacent components, or add unnecessary load to the structure. Conversely, choosing a motor that’s too small may limit torque or thermal capacity, affecting overall performance. In automated systems like robotic arms or gantry setups, minimizing weight is particularly important to maintain speed and reduce strain on other mechanical elements. Compact servo motors with high power density offer a balance between performance and footprint, making them ideal for tight spaces or dynamic operations. Whether you’re designing for an industrial packaging line or a precision assembly station, the right servo motor size ensures optimal system integration without compromising efficiency or reliability.
Mounting Options and Flexibility
Mounting configuration directly affects how easily a servo motor can be integrated into a machine’s mechanical framework. Common mounting types include flange, foot, and face mounts, each catering to different design needs and space constraints. The flexibility to install a servo motor in various orientations—horizontal, vertical, or even inverted—adds to its adaptability across diverse automation setups. For example, a servo motor with multiple mounting holes or adjustable brackets allows quick alignment in systems where space is limited or access is restricted.
In modular industrial automation systems, selecting servo motors with versatile mounting options can simplify design changes, speed up maintenance, and support future scalability. This design flexibility ultimately leads to faster installation and fewer mechanical compromises.
Analyse Cost vs. Performance
Budget Considerations
Selecting the right servo motor often involves balancing technical requirements with budget limitations. While it’s tempting to choose the most advanced option available, doing so can lead to unnecessary expenses if the performance exceeds the actual application needs. Budget-conscious decisions begin with clearly understanding your motion control goals—such as required torque, speed, and precision—and matching them with a cost-effective solution.
For example, a mid-range servo motor may offer more than enough performance for a conveyor system or simple pick-and-place machine, without the premium price tag of high-end models designed for complex multi-axis coordination. Factoring in the cost of associated components—like drives, cables, and feedback systems—is also essential for a realistic total cost assessment. In industrial automation, aligning servo motor selection with both performance and budget helps maximize ROI while ensuring operational goals are met.
Long-Term Efficiency and Reliability
While initial cost is important, long-term performance often determines the true value of a servo motor. Investing in a motor that delivers consistent reliability under demanding conditions can reduce maintenance frequency, prevent unplanned downtime, and lower overall operating costs. High-efficiency servo motors typically use advanced materials, optimized windings, and precision control algorithms to minimize energy consumption and heat generation. Over time, this leads to measurable savings—especially in systems that operate continuously or under heavy loads.
Moreover, choosing a servo motor with proven durability and robust support for industrial automation environments ensures your system stays productive with fewer disruptions. Prioritizing reliability from the outset contributes to a smoother, more cost-effective operation over the motor’s entire lifecycle.