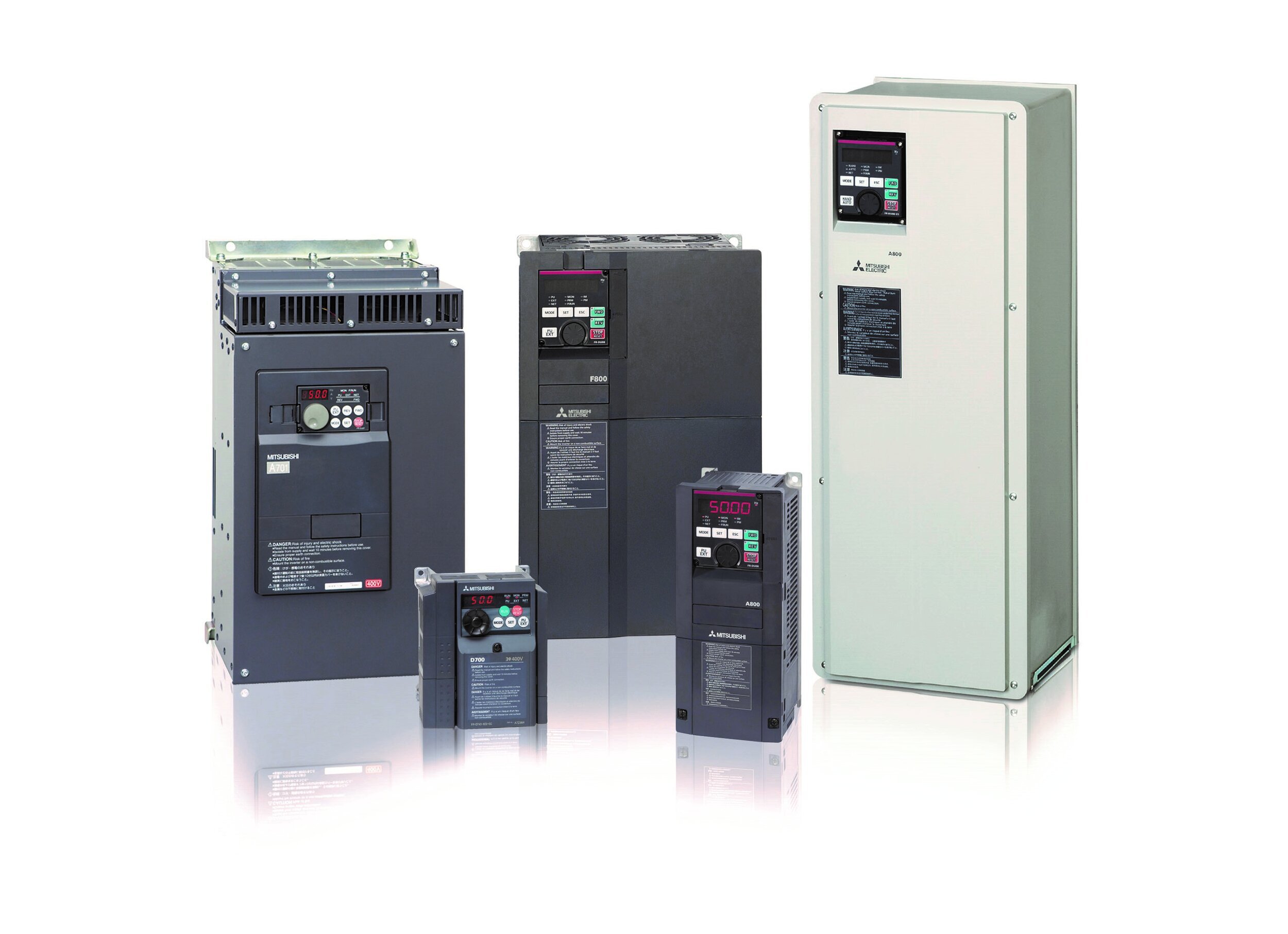
11
Variable Speed Drives Explained: Types, Functions, and the Difference Between VSDs and VFDs
VSDs and VFDs
Definition and Overview.
Variable Speed Drives (VSDs) and Variable Frequency Drives (VFDs) are essential technologies in modern motor control systems, particularly across a wide range of industrial applications. These systems are designed to regulate the speed, torque, and direction of electric motors, helping improve operational efficiency and reduce unnecessary energy consumption.
A Variable Speed Drive (VSD) is a general term that refers to any system capable of controlling the speed of a motor. This includes AC drives, DC drives, and even some mechanical systems. A Variable Frequency Drive (VFD), by contrast, is a specific type of VSD used for AC motors. It controls motor speed by adjusting the frequency and voltage of the electrical power supplied to the motor.
By allowing precise control over motor speeds, both VSDs and VFDs can reduce mechanical stress, extend the lifespan of electrical motors, and contribute significantly to overall energy savings.
Differences Between VSDs and VFDs
Although often used interchangeably, VSDs and VFDs are not the same. The key differences lie in their scope and application.
- VSD is a broad category that includes any drive system used to control motor speeds, whether through electrical, mechanical, or hydraulic means.
- VFD is a specific type of VSD designed exclusively for AC motor control. It alters output frequency and output voltage using electronic switching technology.
For instance, DC motors typically use DC drives (which are a type of VSD), whereas most industrial AC motors are controlled using VFDs. Because of their flexibility and efficiency, VFDs have become a go-to solution in applications that demand precise speed control, improved energy efficiency, and reduced operational costs.
The choice between using a VSD or a VFD depends on the type of motor in use, the control requirements of the application, and whether the system needs to regulate torque, rotational speed, or both.
Importance of VSDs and VFDs in Industry
Motor Control Optimization
In industrial environments, precision is critical—and Variable Speed Drives (VSDs) and Variable Frequency Drives (VFDs) play a central role in optimizing motor control. These systems allow for accurate regulation of motor speeds, making them ideal for applications that require varying load demands or frequent speed adjustments.
By using VFDs, industries gain tighter control over AC motor performance, including rotational speed and torque. This precise control is particularly beneficial in process control systems, where fluctuations in production requirements need responsive and adaptable equipment. For example, in conveyor systems, the ability to ramp speeds up or down ensures smoother operation, reducing mechanical stress on both the motor and the load.
Whether it’s adjusting to fluctuating load requirements or improving response times, VSDs provide consistent and stable operation, extending the life of electrical motors and increasing the reliability of industrial processes.
Enhancing Energy Efficiency
One of the most important advantages of VFDs and VSDs is their contribution to energy efficiency. Traditional motor systems often run at full speed, even when full power isn’t needed—leading to unnecessary energy consumption. VFDs resolve this issue by matching the motor’s output to actual demand, reducing power usage significantly.
This is especially effective in fan, pump, and HVAC applications, where small reductions in motor speed can lead to major energy savings due to the affinity laws. By controlling output frequency and voltage, VFDs allow AC motors to operate only at the speed required for the task, making them a cornerstone of energy-efficient industrial operations.
As industries face increasing pressure to lower their carbon footprint and energy costs, integrating energy-efficient drive systems becomes not just a smart investment, but an operational necessity.
Reducing Operational Costs
The use of VSDs and VFDs directly impacts the bottom line by lowering operational costs. Reduced energy consumption naturally leads to lower electricity bills, but the savings don’t stop there.
By providing smooth motor startup and stopping, VFDs decrease wear and tear on mechanical components. This results in fewer breakdowns, reduced maintenance frequency, and extended equipment life—minimizing unplanned downtime and costly repairs.
In industries where continuous operation is essential, even a brief disruption can lead to significant losses. Implementing variable speed control helps protect the investment in both motors and connected systems, offering not just immediate savings, but long-term cost efficiency as well.
Types of VFDs
Pulse Width Modulation (PWM) Drives
Pulse Width Modulation (PWM) drives are the most common type of Variable Frequency Drives used in industrial motor control today. They work by converting fixed-frequency AC power into DC, and then back into variable-frequency AC power using insulated gate bipolar transistors (IGBTs). This process allows for smooth and efficient control over the speed and torque of AC motors.
PWM VFDs offer precise speed control, improved motor performance, and high energy efficiency. They are widely used across a variety of applications—from pumps and fans to conveyors and mixers—where stable and adjustable speed is essential for both performance and energy savings.
Thanks to their ability to maintain constant torque and minimize harmonic distortion, PWM drives are a preferred solution for most modern industrial applications where accurate motor speed regulation is critical.
Voltage Source Inverter (VSI) Drives
Voltage Source Inverter (VSI) drives are a type of VFD that relies on a DC voltage source, typically supplied through a rectifier, to control the output voltage and frequency delivered to an AC motor. These drives are especially effective in applications that demand high-speed operation and dynamic response.
VSI drives are known for their ability to support a wide range of motor speeds and load conditions while offering excellent efficiency. Commonly used in process automation, HVAC systems, and industrial fans, they allow for seamless integration into modern motor control setups.
In addition to delivering reliable motor speed control, VSI drives can also reduce mechanical wear by providing smoother starts and stops, which helps extend the service life of equipment and motors.
Current Source Inverter (CSI) Drives
Current Source Inverter (CSI) drives differ from VSI drives in that they use a constant current input instead of constant voltage. These drives are typically used in high-power industrial applications where motor loads are large and require precise torque control.
CSI drives are ideal for driving synchronous motors and large induction motors in heavy-duty environments such as mining, metal processing, and marine propulsion. Their robust design enables them to handle challenging conditions and deliver consistent performance under variable load requirements.
Although less common than VSI or PWM drives, CSI drives offer significant advantages in specific scenarios that demand high torque, continuous operation, and resilience to electrical disturbances.
Advanced Control Methods
Flux Vector Control Techniques
Flux vector control is an advanced method used in modern Variable Frequency Drives (VFDs) to achieve high-performance motor control, particularly for applications that demand precise torque and speed regulation. Unlike traditional VFDs that adjust motor speed based solely on voltage and frequency, flux vector control uses complex algorithms to manage both the magnetic flux and the torque-producing current in the motor.
This technique transforms how electric motors respond under varying loads, making it highly effective for applications such as cranes, elevators, extruders, and other systems where maintaining torque at low speeds is critical. By simulating a DC motor’s performance, flux vector control delivers rapid dynamic response and better control over motor torque.
VFDs with flux vector control are commonly used in industrial settings that require superior accuracy and stability, offering enhanced energy efficiency and smoother mechanical operation even under heavy-duty conditions.
Sensorless Vector Control Precision
Sensorless vector control is another sophisticated motor control method found in advanced VFD systems. It provides most of the benefits of traditional vector control—such as precise motor speed and torque control—without the need for external feedback devices like encoders or resolvers.
Instead, sensorless vector control uses mathematical models and internal monitoring to estimate motor parameters in real time. This makes it a cost-effective solution for applications that still require high-performance operation but where adding a physical sensor may be impractical or too expensive.
Typical uses include industrial fans, pumps, compressors, and conveyor systems, where performance demands are high but operational simplicity and reliability are also important. Sensorless vector control improves energy savings and motor efficiency, offering precise control over motor speed even when load conditions fluctuate.
By eliminating the need for feedback sensors, these drives reduce installation complexity while still delivering accurate and responsive control for a wide range of industrial applications.
Practical Applications of VSDs and VFDs
Conveyor belt systems are one of the most common industrial applications for Variable Speed Drives (VSDs) and Variable Frequency Drives (VFDs). These systems benefit greatly from the precise speed control and smooth acceleration that VFDs provide, which is essential for handling delicate materials or synchronizing with other stages in a production line.
By adjusting motor speeds in real time, VSDs help prevent mechanical stress and reduce wear on belts and drive components. This not only extends the life of the equipment but also improves the consistency and reliability of material flow. Whether moving heavy loads in mining operations or handling packaging lines in food production, VFDs ensure efficient and responsive operation.
Heating, Ventilation, and Air Conditioning (HVAC) systems rely heavily on VFDs to optimize energy consumption and maintain consistent environmental conditions. In HVAC fan and compressor applications, VFDs allow motors to operate at variable speeds depending on the actual load, rather than running continuously at full capacity.
This adaptability significantly reduces energy usage, especially during periods of low demand. For example, adjusting fan speeds in response to room occupancy or external temperature helps maintain comfort while cutting down on electricity costs. The result is a more energy-efficient building system with improved environmental control and reduced operational expenses.
Using VFDs in HVAC systems also supports smoother motor startup and shutdown, minimizing mechanical stress and enhancing long-term reliability—an essential factor in commercial and industrial buildings.
Pump and fan systems are ideal candidates for VFD integration due to their variable load requirements. In traditional setups, motors run at constant speed, even when full output isn’t necessary. This leads to excessive energy consumption and unnecessary strain on system components.
VFDs solve this by modulating the output frequency and voltage based on the actual process demand. For instance, in water supply systems, a VFD can adjust pump speed based on real-time pressure or flow data, ensuring just the right amount of energy is used. Similarly, in ventilation or cooling applications, fan speeds can be fine-tuned to meet environmental or process needs.
By matching motor output to system requirements, VFDs significantly reduce energy waste, improve process control, and contribute to more sustainable industrial operations.
Advanced Control Method
Flux Vector Control Techniques
Flux vector control is an advanced method used in modern Variable Frequency Drives (VFDs) to achieve high-performance motor control, particularly for applications that demand precise torque and speed regulation. Unlike traditional VFDs that adjust motor speed based solely on voltage and frequency, flux vector control uses complex algorithms to manage both the magnetic flux and the torque-producing current in the motor.
This technique transforms how electric motors respond under varying loads, making it highly effective for applications such as cranes, elevators, extruders, and other systems where maintaining torque at low speeds is critical. By simulating a DC motor’s performance, flux vector control delivers rapid dynamic response and better control over motor torque.
VFDs with flux vector control are commonly used in industrial settings that require superior accuracy and stability, offering enhanced energy efficiency and smoother mechanical operation even under heavy-duty conditions.
Sensorless Vector Control Precision
Sensorless vector control is another sophisticated motor control method found in advanced VFD systems. It provides most of the benefits of traditional vector control—such as precise motor speed and torque control—without the need for external feedback devices like encoders or resolvers.
Instead, sensorless vector control uses mathematical models and internal monitoring to estimate motor parameters in real time. This makes it a cost-effective solution for applications that still require high-performance operation but where adding a physical sensor may be impractical or too expensive.
Typical uses include industrial fans, pumps, compressors, and conveyor systems, where performance demands are high but operational simplicity and reliability are also important. Sensorless vector control improves energy savings and motor efficiency, offering precise control over motor speed even when load conditions fluctuate.
By eliminating the need for feedback sensors, these drives reduce installation complexity while still delivering accurate and responsive control for a wide range of industrial applications.
Â
Practical Applications of VSDs and VFDs
Conveyor Belt Systems
Conveyor belt systems are one of the most common industrial applications for Variable Speed Drives (VSDs) and Variable Frequency Drives (VFDs). These systems benefit greatly from the precise speed control and smooth acceleration that VFDs provide, which is essential for handling delicate materials or synchronizing with other stages in a production line.
By adjusting motor speeds in real time, VSDs help prevent mechanical stress and reduce wear on belts and drive components. This not only extends the life of the equipment but also improves the consistency and reliability of material flow. Whether moving heavy loads in mining operations or handling packaging lines in food production, VFDs ensure efficient and responsive operation.
HVAC Systems
Heating, Ventilation, and Air Conditioning (HVAC) systems rely heavily on VFDs to optimize energy consumption and maintain consistent environmental conditions. In HVAC fan and compressor applications, VFDs allow motors to operate at variable speeds depending on the actual load, rather than running continuously at full capacity.
This adaptability significantly reduces energy usage, especially during periods of low demand. For example, adjusting fan speeds in response to room occupancy or external temperature helps maintain comfort while cutting down on electricity costs. The result is a more energy-efficient building system with improved environmental control and reduced operational expenses.
Using VFDs in HVAC systems also supports smoother motor start-up and shutdown, minimizing mechanical stress and enhancing long-term reliability—an essential factor in commercial and industrial buildings.
Pump and Fan Systems
Pump and fan systems are ideal candidates for VFD integration due to their variable load requirements. In traditional setups, motors run at constant speed, even when full output isn’t necessary. This leads to excessive energy consumption and unnecessary strain on system components.
VFDs solve this by modulating the output frequency and voltage based on the actual process demand. For instance, in water supply systems, a VFD can adjust pump speed based on real-time pressure or flow data, ensuring just the right amount of energy is used. Similarly, in ventilation or cooling applications, fan speeds can be fine-tuned to meet environmental or process needs.
By matching motor output to system requirements, VFDs significantly reduce energy waste, improve process control, and contribute to more sustainable industrial operations.
Energy Consumption and Environmental Impact
Reducing Energy Costs
One of the most significant advantages of using Variable Speed Drives (VSDs) and Variable Frequency Drives (VFDs) in motor-driven systems is the substantial reduction in energy costs. Traditional motors often run at a constant speed regardless of actual demand, leading to excess energy use and inflated electricity bills. VFDs resolve this inefficiency by adjusting motor speeds according to real-time load requirements.
For example, in pump and fan applications, even a small reduction in speed can lead to dramatic energy savings, thanks to the nonlinear relationship between speed and power consumption defined by the affinity laws. By avoiding unnecessary power usage, VFDs reduce operational costs while also extending the lifespan of electrical motors.
Industries operating large-scale motor systems—such as manufacturing, water treatment, and mining—stand to benefit greatly from the long-term cost efficiencies that energy-saving drives deliver.
Implications for Emission Reductions
In addition to cost savings, VSDs and VFDs also have a positive environmental impact. By improving energy efficiency and lowering overall electricity consumption, these drives help reduce the demand on power plants—many of which still rely on fossil fuels. The result is a decrease in greenhouse gas emissions and other pollutants associated with industrial energy use.
In sectors where sustainability is becoming a strategic priority, integrating VFDs into AC motor systems supports emission reduction goals and regulatory compliance. For example, facilities aiming to meet ISO 50001 or other energy management standards often adopt VFDs as part of their efficiency initiatives.
Beyond regulatory benefits, reducing energy consumption and emissions also aligns with corporate responsibility objectives, helping businesses operate more sustainably while maintaining high levels of productivity.
Key Factors for Maintenance
Regular Inspection and Servicing
To ensure long-term reliability and optimal performance, Variable Speed Drives (VSDs) and Variable Frequency Drives (VFDs) require consistent maintenance through regular inspection and servicing. These drives are central to motor control in many industrial applications, and neglecting their upkeep can lead to unplanned downtime, reduced energy efficiency, and costly repairs.
Routine inspections should focus on checking electrical connections, monitoring output voltage stability, and ensuring that cooling systems—such as fans and heat sinks—are free of dust or obstruction. Overheating due to clogged airflow is a common issue that can reduce drive lifespan and disrupt speed control functions.
In environments with fluctuating loads or high operational demand, periodic software diagnostics can help detect faults early and ensure that control parameters remain optimized. Proactive maintenance not only enhances operational efficiency but also safeguards the performance of the motors connected to the drive system.
Component Replacement Strategies
Even with consistent servicing, some VFD components will naturally degrade over time. Implementing a smart component replacement strategy helps maintain reliability without waiting for failures to occur. Critical components like capacitors, cooling fans, and IGBT modules are subject to wear and should be replaced based on manufacturer recommendations or operational hours.
For example, electrolytic capacitors tend to degrade with thermal stress and age, which can affect output frequency stability and result in erratic motor speed control. Replacing these components at set intervals ensures that the drive continues to operate within its specified performance range.
In high-demand industrial systems, planning for scheduled replacements—rather than reactive fixes—helps prevent costly downtime and extends the overall life of the VFD. Maintaining detailed maintenance records and aligning them with the specific load requirements of each application ensures both energy-efficient performance and consistent motor control.
Future Trends and Developments
Integration with Smart Technologies
As industrial operations continue to evolve, Variable Speed Drives (VSDs) and Variable Frequency Drives (VFDs) are increasingly being integrated into smart technology ecosystems. The rise of Industry 4.0 and the Industrial Internet of Things (IIoT) is reshaping how drive systems operate, communicate, and optimize performance.
Modern VFDs now come equipped with built-in communication protocols such as Modbus, EtherNet/IP, and PROFINET, enabling real-time data exchange with programmable logic controllers (PLCs) and cloud-based monitoring systems. This connectivity allows operators to remotely monitor motor speeds, energy consumption, output voltage, and system faults—driving smarter decisions and predictive maintenance strategies.
By leveraging data analytics and automation, these advanced drives contribute to greater energy efficiency, reduced downtime, and streamlined process control. Their ability to adapt dynamically to changing load requirements makes them integral to the next generation of industrial motor control systems.
Innovations in Drive Technology
Technological advancements continue to push the boundaries of what VFDs can achieve. New developments are focused on increasing precision, energy efficiency, and reliability across a wider range of industrial applications. For instance, improvements in semiconductor materials and switching algorithms are allowing drives to operate at higher frequencies with less heat generation and greater control over motor torque and speed.
Sensorless vector control has also advanced significantly, providing near closed-loop performance without requiring external sensors. Additionally, newer VFD models are being designed with compact form factors, modular architectures, and intuitive user interfaces that simplify installation and operation.
As industries move toward sustainability, VFDs are also being optimized for renewable energy integration, helping manage variable power inputs and maximize the efficiency of systems powered by solar or wind sources.
These innovations reflect a broader trend: VFDs are not only supporting existing industrial processes—they’re actively shaping the future of smart, efficient, and sustainable motor control.
Our VSD Featured Products
- Mitsubishi Parameter Unit Connection Cable 1m FR-CB20-L1
- 22kW Mitsubishi FR-XCL-H22K Stand-alone Reactor 400V | Mitsubishi Products
- Mitsubishi FR-E8CN05 E840 2.2K 3.7K Panel Attachment for Heat Dissipation
- Mitsubishi 11kW Inverter FR-D720-11K 100% Rated 45A, Overload 150% 65.5A
- Mitsubishi 0.4kW Inverter FR-A840-00023-E260 | EMC Compliant, Ethernet
- Mitsubishi FR-PU07: Parameter Unit for remote control
- High-Quality Mitsubishi FR-A8APA SinCos Encoder Feedback for FR-A800
- Mitsubishi 1.5kW Inverter FR-A820-00105-2-60 with RS-485 Interface
- 90kW EMC-Compliant Mitsubishi Inverter FR-A840-02600-2-60 with RS-485
- Mitsubishi FR-D720S-0.2K-EC 0.2kW Inverter with EMC Filter & Overload Capacity