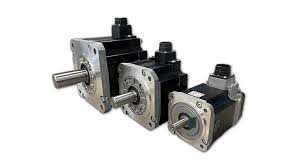
1
Understanding Servo Motor Noise Sources
Understanding Servo Motor Noise Sources
Servo motor noise is more than just a nuisanceāit can signal deeper issues within your automation system. Whether caused by mechanical imbalance, electrical interference, or environmental conditions, excess noise affects performance, precision, and long-term reliability. Understanding the root causes and implementing effective noise reduction techniques is essential for keeping your motion control systems operating at peak efficiency.
If you’re new to the topic, start by exploring what a servo motor is and how it works to understand the fundamentals. Regular servo motor maintenance plays a key role in noise prevention and performance stability. For real-world applications, our guide on servo motor uses in automation highlights where noise control is most critical. To support system-wide reliability, consider pairing your servo setup with Mitsubishi Electric PLCs or networking with CC-Link systems, both designed to minimize interference and optimize communication. For added safety and compliance, safety light curtains help ensure protection without introducing mechanical complexity that can contribute to excess noise.
Mechanical Noise Causes
Mechanical noise in servo motors often originates from physical interactions within the motor or the broader motion system. One common cause is misalignment between the motor shaft and the load, which can introduce vibration and excess friction. Over time, this not only generates noise but can also lead to premature wear of bearings and couplings.
Loose mounting hardware is another frequent culprit. Even minor looseness in motor mounts, gear assemblies, or base plates can result in rattling or resonant noise during operation, especially under varying loads. Similarly, worn or poorly lubricated bearings can produce grinding or humming sounds, particularly at high speeds.
In high-precision automation environments, mechanical imbalancesāsuch as uneven mass distribution on rotating partsācan also trigger servo motor noise. These imbalances disrupt smooth motion control and may amplify during acceleration or deceleration phases.
To minimize mechanical noise in servo motor systems, ensure proper alignment, secure all components tightly, and maintain consistent lubrication schedules. Selecting high-quality mechanical components with tight tolerances can also reduce vibration-related issues.
Electrical Noise Causes
Electrical noise in servo motors typically stems from interference within the motorās control and power circuitry. One key source is electromagnetic interference (EMI) generated by rapidly switching signals in servo drives. This can affect not only the servo motor itself but also nearby automation components, leading to erratic behavior or signal loss.
Another common cause is improper grounding or shielding of cables. Inadequate shielding allows high-frequency signals from the servo drive to radiate and couple into other circuits, especially in dense industrial environments. This is particularly problematic in systems with long cable runs or where servo motors are integrated with sensitive electronics.
Pulse-width modulation (PWM), used to control motor speed and torque, can also contribute to electrical noise. High switching frequencies, while beneficial for smoother motion, tend to increase noise levels unless managed carefully with filtering techniques.
To reduce electrical noise, use shielded cables with proper grounding at one end, route power and signal lines separately, and apply ferrite cores or filters where needed. Ensuring the servo driveās configuration matches the motorās electrical characteristics is also essential for minimizing noise and maintaining motion precision.
Mechanical Noise Reduction Techniques
Ensuring Proper Alignment
Improper alignment between the servo motor and the driven load is a leading cause of mechanical noise and vibration in motion control systems. When shafts are misalignedāeither angularly or axiallyāthey create uneven torque loads, which can generate audible chatter or oscillation during operation.
Using precision alignment tools, such as laser alignment systems or dial indicators, helps ensure the motor shaft is perfectly aligned with the load. This is especially critical in servo motor applications where high-speed rotation and tight tolerances demand smooth, uninterrupted motion. In automated machinery, even slight misalignment can compromise positioning accuracy and increase wear on couplings and bearings, further contributing to servo motor noise.
Regular inspection and realignment during scheduled maintenance can help prevent issues before they impact performance.
Addressing Bearing Failures
Bearing failure is another significant source of mechanical noise in servo motors. Over time, bearings may degrade due to improper lubrication, contamination, or excessive load, resulting in grinding, humming, or rattling sounds. In high-speed or continuous-duty applications, these symptoms often point to worn races or pitting on the bearing surfaces.
Preventing servo motor bearing noise starts with selecting high-quality, sealed bearings suited to the operating environment. Proper lubrication intervals must be maintained, and for harsh industrial settings, using bearings with enhanced sealing or ceramic options may improve durability and reduce vibration.
Monitoring bearing temperature and vibration levels through predictive maintenance can also help catch early signs of failure, minimizing unplanned downtime and preserving the motorās long-term performance.
Balancing Load Distribution
Uneven load distribution can introduce instability and increase noise levels during servo motor operation. When mechanical loads are offset or imbalanced, the motor must work harder to compensate, leading to fluctuating torque and additional stress on components.
This is particularly evident in systems with rotating assembliesālike conveyors or robotic armsāwhere an unbalanced mass can cause vibration and audible rumbling. For servo-driven equipment, unbalanced loads also reduce motion efficiency and shorten component lifespan.
Ensuring symmetrical load placement and verifying that mounting surfaces are level and rigid helps maintain balance. In more complex applications, dynamic balancing of rotating elements may be necessary to eliminate inconsistencies. For OEMs and integrators, accounting for load distribution during the design phase can significantly reduce the potential for mechanical noise once the system is operational.
Electrical Noise Mitigation Strategies
Using Shielded Cabling
Shielded cabling plays a crucial role in reducing electrical noise in servo motor systems. As servo drives generate high-frequency switching signals, unshielded cables can radiate electromagnetic interference (EMI), which disrupts nearby control signals and degrades system performance.
By enclosing conductors in a grounded metallic shield, shielded cables prevent EMI from escaping or entering sensitive circuits. This is especially important in industrial automation environments, where multiple servo motors, sensors, and PLCs operate in close proximity. For example, in a servo-driven conveyor system, using shielded motor and feedback cables helps maintain accurate communication between the drive and controllerāeven in electrically noisy settings.
To maximize effectiveness, the shield should be grounded at one end only, typically at the drive side, to prevent circulating currents that can introduce additional noise.
Eliminating Ground Loops
Ground loops occur when multiple ground paths create unintended current flows, leading to voltage fluctuations and unwanted electrical noise. In servo motor applications, ground loops can interfere with encoder signals or cause erratic drive behavior, particularly in systems with long cable runs or interconnected equipment.
Preventing ground loops starts with establishing a single-point ground reference for the entire system. This ensures all componentsāservo drives, motion controllers, and power suppliesāshare a common ground potential. Avoiding connections between multiple ground paths minimizes differential voltage and reduces the likelihood of induced noise.
Using isolated power supplies and signal conditioners can also help eliminate ground loop effects, especially in systems that connect to external sensors or third-party automation devices.
Optimizing Network Configurations
A well-structured network configuration is essential for maintaining clean communication between motion controllers, servo drives, and other automation components. Poor network topology or excessive cable lengths can lead to signal degradation, data collisions, and increased electrical noise, particularly in high-speed industrial networks like EtherCAT or Modbus TCP.
To reduce noise-related communication issues, servo systems should use properly terminated cables and adhere to manufacturer-recommended network layouts. Star or daisy-chain configurations should be implemented with care, ensuring each deviceās communication port is used appropriately.
Segmenting control and power lines, assigning unique IP addresses or device IDs, and enabling error-checking protocols can further stabilize network performance. In multi-axis motion control setups, optimizing network timing and minimizing latency helps keep servo motors synchronized, improving both precision and noise immunity.
Environmental Modifications
Controlling Ambient Temperature
Ambient temperature has a direct impact on the performance and noise levels of servo motors. When operating in environments that exceed the motorās recommended temperature range, components such as bearings, insulation, and lubricants degrade faster. This not only affects longevity but can also lead to increased mechanical noise due to thermal expansion and material fatigue.
To keep servo motor systems running smoothly, it’s essential to maintain a stable operating temperature. This can be achieved through proper ventilation, the use of industrial cooling fans, or enclosing motors in climate-controlled panels. In high-temperature industrial zones, heat shields or forced-air cooling systems help prevent overheating, reducing both acoustic noise and the risk of motor failure.
Temperature management is especially critical in continuous-duty applications or enclosed automation cabinets, where heat buildup can be significant.
Reducing Vibrations in the Environment
Environmental vibrations can transfer into servo motor systems, leading to erratic movement and added noise. These external sourcesāsuch as nearby heavy machinery or unstable mounting platformsācan resonate through the structure and interfere with precise motion control.
Minimizing vibration begins with proper machine isolation. Using vibration-dampening mounts, rigid bases, and shock-absorbing pads can significantly reduce the transmission of environmental vibration into the servo system. This is particularly important in high-precision setups, like CNC machines or robotic arms, where even minor disturbances can cause performance issues.
Locating servo motors away from high-vibration zones and securing all associated components tightly ensures that the system remains stable, quiet, and reliable during operation
Using Noise Dampening Materials
Integrating noise dampening materials into the environment is an effective strategy for reducing overall acoustic emissions from servo motor systems. These materials work by absorbing or deflecting sound waves, limiting how far mechanical or electrical noise can travel within a facility.
Common solutions include acoustic foam panels, vibration-isolating mats, and sound-dampening enclosures. For example, placing servo-driven machinery on rubber isolation pads can reduce both transmitted vibration and noise. In automated manufacturing lines, lining control cabinets or surrounding high-speed motors with acoustic insulation helps keep noise levels within acceptable thresholds.
Selecting materials with high noise reduction coefficients (NRC) ensures better absorption, making them ideal for environments where multiple servo motors are in use. This not only improves workplace comfort but also supports compliance with industrial noise regulations.
Advanced Noise Reduction Technologies
Active Noise Control Systems
Active noise control (ANC) systems represent a modern approach to minimizing servo motor noise, especially in high-performance environments. Unlike passive methods that rely on physical barriers or insulation, ANC uses real-time signal processing to cancel out unwanted sound waves. By generating inverse sound waves that directly oppose detected noise, these systems effectively reduce acoustic disturbances at their source.
In servo motor applications, active noise control is particularly useful in enclosed machinery or robotics where precision and quiet operation are essential. For instance, in medical automation or semiconductor manufacturing, ANC helps maintain low-noise environments without sacrificing motor responsiveness or speed.
These systems typically incorporate microphones, digital signal processors, and speakers, working together to continuously monitor and suppress unwanted mechanical or electrical noise. As servo motors become more prevalent in noise-sensitive industries, ANC solutions are increasingly being integrated into equipment designs for optimal motion control performance.
Noise Filtering Equipment
Noise filtering equipment is critical for maintaining signal integrity and reducing electrical interference in servo motor systems. High-frequency switching from servo drives can generate significant electromagnetic noise, which disrupts communication lines and leads to performance instability if not properly managed.
To combat this, industrial automation setups often use a combination of line filters, ferrite beads, and EMI suppression devices. Line filters installed between the power supply and the servo drive block unwanted frequencies, while ferrite cores clamped around cables help suppress high-frequency noise without affecting signal transmission.
Additionally, specialized filters for encoder lines or analog input channels can prevent electrical noise from corrupting feedback signals, ensuring accurate motion control. Integrating these noise filtering components not only enhances servo system reliability but also helps meet compliance standards for electromagnetic compatibility (EMC) in industrial environments.