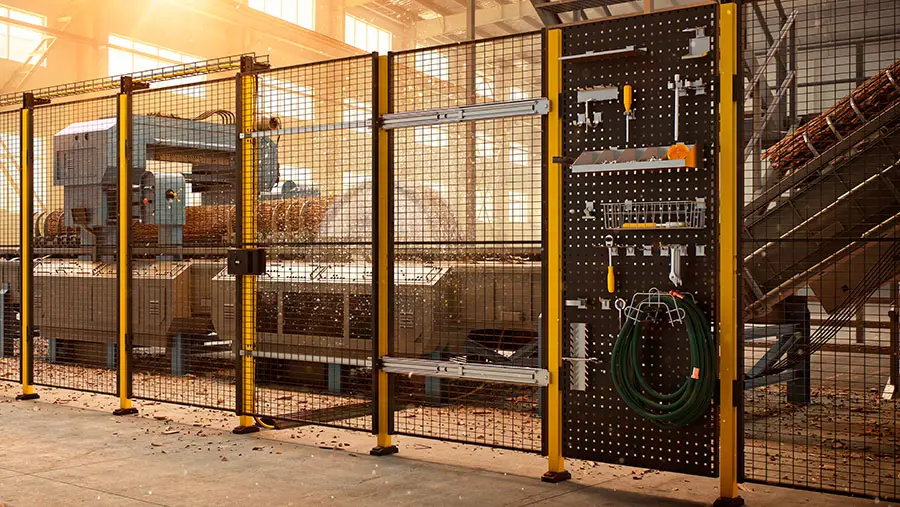
19
On The Fence About Machine Guarding? Let’s Make The Switch!
Machine guarding overview
When considering hazardous areas on machines such as crushing/impact, entanglement, laceration, stabbing, and abrasion hazards, it is important to understand two main ways to guard operators from interacting with them. The first option, which we have discussed extensively, are electro-mechanical solutions. These include electrical interlocks, mechanical interlocks, safety switches (both contact, and non-contact), and photoelectric sensors.
The second, often more simple solutions lie within permanent and fixed guarding.
Permanent machine guarding, as the name would suggest, is an inherent guard built into the design of a hazardous machine. For example, an AC motor has a spinning shaft that is hazardous once it reaches its operating speed. They can pinch, cut (if there are blades/gears), and generally harm operators. To mitigate this, a metal sheet welded onto a machine to form a barrier, or housings between a motor and a gearbox, would make the shaft of an AC motor inaccessible when assembled. Permanent guards are integrated into the design and cannot be removed.
Generally speaking, the use of permanent guards in hazardous areas is not feasible if the machinery contains serviceable parts and thus requires maintenance.
This is where fixed guarding becomes valuable. Fixed guards are considered as semi-permanent physical barriers between operators and hazards. They include fencing, tunnel guards, or roller cover guards. If these fixed guards are not interacted with frequently, this form of fixed guarding is sufficient. However, in the case of access doors, panels, gates, and moving guards that allow conditional access to a hazard (it should not open when the machine is running), interlocked guards are required.
This blog post will briefly explore some machine guarding options—two fixed, and two interlocked.
Fencing is a crucial form of fixed guarding in the industrial workplace. Fixed guarding through fences and barriers prevent access to hazardous machinery and prohibit operator-machine interactions during dangerous operations. By creating a physical barrier, fencing ensures that workers maintain a safe distance from hazards brought about by moving heavy machinery.
There are different types of fences, including perimeter fences and distance guards, which are strategically positioned to limit one’s reach into a hazard. Furthermore, horizontal and vertical spacing of mesh is also a factor that is considered by fence guarding designers. Reaching in through a grille, and through square/circular apertures (the gaps in fences) all have acceptable and expected measurements such as the distance from the danger point (safety distance), along with the separation between each line of fencing.
Beyond this, fixed guard fencing with access points may also be designed to limit movement from operators so that entry of a limb into a hazardous area is restricted. Examples of this would be adding an arm support that extends to joints depending on the angle/range of the hazard. For example, these guards can support up to the knuckle joint, the wrist joint, or the shoulder joint.
Fences are often installed based on reach distances—guidelines that determine the minimum safe distance from the hazard based on ergonomic factors and the likelihood of someone attempting to lean over or reach through the fence.
Axelent’s X-Guard safety fencing system is a versatile and modular solution designed to meet the latest safety standards, including the Machinery Directive 2006/42/EC. This system offers various configurations for effective machine guarding, including mesh panels, posts, and door options (hinged or sliding). It ensures comprehensive perimeter protection, preventing access to hazardous areas while maintaining visibility and accessibility for maintenance.
Additional accessories, like cable trays, enhance functionality and installation efficiency, making X-Guard an adaptable choice for industrial environments.
Fixed Guards - Axelent Fencing
Fixed Guards - Concertina Roller Guards
Another option for fixed guarding that presents itself in industry is roller guards. Roller guards are ideal for tight, limited spaces, and are also capable of expanding (and locking in place) and retracting. This enhances the flexibility of these guards, enabling hazardous areas and environmentally sensitive moving parts to be effectively fenced-off from operators. However, since they can retract, Concertina guards do not limit the ability for operators to remove the cover guards to carry out maintenance on any serviceable parts.
Commonly used on fitting, turning, and CNC machine tools, Concertina guards are a durable ‘curtain’ type of guard that shield contaminants like dust, debris, and corrosive/caustic liquids from entering sensitive machines and sensors. When rolled up, Concertina guards are compact and low-profile; but can always be expanded into their full size. Typically comprised of a metal (most likely aluminium or steel) housing and coated fabric, Concertina guarding is chemically inert, and resistant to oils, acidic, and basic liquids. The end tabs of each roller are often some form of metal cladding, enabling the guards to be bolted into a desired spot for more permanent guarding, while also providing protection from the edges of the roller fabric from fraying.
Enhancing their flexibility even further, Concertina roller guards are made to customer specifications, allowing them to be made to suit whatever measurements and spaces the customer requires. Overall, this form of fixed guarding ensures cleanliness, precision, and safety of machine operation. Concertina roller guards contribute greatly to workplace safety by barring operators from hazardous parts.
Machine Guarding: two-hand controls
Introduction
When fixed guarding is less viable/sufficient to protect workers from hazards, different approaches need to be taken to guard operators in other ways. Not unlike fixed guarding methods, some electro-mechanical safety solutions also aim to inhibit the movement of machine operators.
To achieve this, two-hand control systems have been developed. Similar to AND gates in Boolean logic, a two-hand control needs an operator to depress both buttons to enable continuity of power flow. Similar to fencing or roller guards, a two-hand control restricts the movement of an operator to only within a tight radius around the machine.
Typical Applications
Typical applications for two-hand controls as a form of machine guarding include:
- Hydraulic presses, punches, and stamping procedures
- Cutting equipment such as automated shears/guillotines
- Packaging/clamping/sealing machinery
- Press brakes and metal bending machinery
- Injection moulding machines
Two-hand controls are useful when an operator’s involvement is essential to start/stop a machine; enhancing safety by enforcing deliberate engagement from a safe distance.
Limitations
Limited Hazard Protection: While two-hand controls do ensure that an operator’s hands are kept safe, it is important to understand that these control panels on their own will not protect against other risks like unintended machine startups, unexpected ejection of materials, and hazards that threaten other body parts of the operator.
Limited Operator Protection: Two-hand controls, as the name suggests, are limited to only making sure two hands are in a safe location. So, what about in the case of multiple workers needing to be kept safe? Well, in that case, a two-hand control is unlikely to protect the majority of workers and hazards that present themselves. This is where further security is needed and can be achieved through mechanical interlocks.
Safety Mechanical Interlocks: an overview
Introduction
When it comes to machine guarding, sometimes fixed guard is designed so that it remains closed and in place when running, but can be opened and accessed when the machine is off. So, for areas that are only hazardous during machine operation, implementations such as mechanical interlocks have been made for enhanced safety. Mechanical interlocks are one of a few ways that gates, guards, and hinged/sliding doors can be protected. Mechanical interlocks often involve some kind of receiver (this stays on the part that sits still), while there is a freely moving insert (this goes on the hinged/rolling section of the door). Using contacts, sensors, and other forms of switching devices, a mechanical interlock detects whether it is whole (and thus the door is closed) or not. In the case of mechanical interlocks configured to work with a safety relay or PLC, the presence of the insert in the receiver can be used as a safety input into the logic controller.
Using the open/closed state of the door, the logic controller can use this condition to either enable or disable machine operation. Some interlocks receive power to release (power-to-unlock) while others require power to remain locked (power-to-lock). Can you guess which one is of a higher safety rating? By receiving power-to-unlock, any sudden power loss would ensure safety, keeping the door locked. Meanwhile, a power-to-lock interlock would allow any door to be opened if it were to lose power.
Most mechanical interlocks are offered in high levels of strength, environmental resistance, and fail-safe locking mechanisms to remain secure. Using heavy-duty thermoplastics, metal alloys, or stainless steels, safety mechanical interlocks ensure great tolerance to exposure to the elements. Some mechanical interlocks are even offered with tamper-resistant housings. For example, some interlocks from Pizzato include an RFID-coded transmitter and receiver along with the insert and receiver. This now means that the tongue has to be present, but also the RFID emitter and receiver have to be aligned to allow the machine to register that the gate is closed, locked, and safe to allow operation.
Security
Interlocks are a highly valuable tool in automated assembly lines. Constructed from durable materials and enhanced in safety by using dual channel outputs, they are a way to guarantee that doors are closed and secured during automated operations. Furthermore, interlocks such as these can interface directly with relays and other safety devices, making them easy to integrate.Â
Modularity
What is incredibly useful about some mechanical interlocks for machine guarding is the fact that interlocks can be used in series. The output of one interlock can go into the input of the next, and so on and so forth. This means that a series, and perhaps whole/multiple assembly line’s worth of interlocks can all be used as a series input into one set of channels of a safety relay, while still maintaining a high safety rating.Â
Plastic Body Mechanical Interlock Switches Overview
Plastic body mechanical interlock switches are designed to secure access points and protect operators from hazardous machinery. These interlocks use high-strength plastic materials, making them lightweight yet durable, with excellent resistance to moisture, dust, and corrosion. While metal interlocks are suited for heavy-duty applications, plastic interlocks are ideal for applications where weight, cost, and moderate environmental resilience are key factors. They offer reliable safety features while maintaining cost-effectiveness, making them a preferred choice in various industries.
The Importance of Plastic Body Mechanical Interlock Switches in Safety
In the safety industry, interlock switches are vital in machine guarding systems. Plastic body interlocks ensure that safety protocols are enforced, securing doors, gates, and access panels, thus preventing accidental exposure to hazardous zones. Their lightweight design and corrosion-resistant material make them suitable for environments where electrical insulation and flexibility are required, such as food processing, pharmaceutical, and electronic manufacturing facilities.
Applications of Plastic Body Mechanical Interlock Switches
Plastic body mechanical interlock switches are widely used in industries such as manufacturing, automotive, electronics, and food processing. Common applications include:
- Access Control for Light Machinery: Securing access points to equipment where heavy-duty interlocks are not necessary.
- Food Processing and Pharmaceuticals: Providing safety in environments that require resistance to water, cleaning agents, and chemicals.
- Automotive and Electronics: Ideal for conveyor systems and assembly lines where weight reduction and electrical insulation are essential.
- Cleanrooms: Used to secure doors and gates while maintaining cleanliness and hygiene standards.
Metal Body Mechanical Interlock Switches Overview
Metal body mechanical interlock switches are crucial safety devices designed to monitor and control access to potentially hazardous areas in industrial environments. Constructed with a robust metal casing, these switches are engineered for durability and resilience in harsh settings, providing a reliable solution for safeguarding personnel and equipment. These switches operate by mechanically interlocking safety gates, doors, or access panels, ensuring that dangerous machinery remains inaccessible when unsafe conditions are detected.
The Importance of Metal Body Mechanical Interlock Switches in Safety
In the safety industry, interlock switches are essential components of machine guarding systems, reducing the risk of accidental injury by preventing unauthorized access to hazardous zones. These switches play a pivotal role in complying with safety standards and regulations, as they enforce safety protocols and help prevent human errors, which are a leading cause of workplace accidents.
Applications of Metal Body Mechanical Interlock Switches
Metal body mechanical interlock switches are widely used in sectors such as manufacturing, automotive, pharmaceuticals, and food processing, where safeguarding machinery and maintaining operational safety are paramount. Common applications include:
- Assembly Line Safety: Preventing access to moving parts in conveyor systems or assembly lines until all operations have ceased.
- Machine Guarding: Ensuring operators cannot access or adjust machinery while it is in operation, especially in settings with high-speed or high-torque equipment.
- Robotic Cells: Securing entry points to robotic work cells to prevent injury during automated operations.
- Food and Pharmaceutical Processing: Maintaining hygiene standards and protecting operators from equipment used in processing and packaging.
- Heavy Industry and Mining: Withstanding the rigors of challenging environments where switches are exposed to heavy loads, dust, moisture, and high temperatures.
Stainless Steel Mechanical Interlock Switches Overview
Stainless steel mechanical interlock switches are designed for use in highly demanding environments where durability, corrosion resistance, and hygiene are essential. These switches feature robust stainless steel casings, which make them resistant to harsh chemicals, moisture, and high temperatures. Their construction provides superior strength and longevity, ensuring reliable safety performance in settings that require regular cleaning or exposure to aggressive substances. Stainless steel interlocks are ideal for applications where plastic or standard metal interlocks might fail or degrade over time.
The Importance of Stainless Steel Mechanical Interlock Switches in Safety
Stainless steel mechanical interlocks play a critical role in maintaining safety and compliance in industries where extreme conditions are present. The corrosion-resistant properties of stainless steel make these interlocks essential for sectors such as food and beverage, pharmaceuticals, and chemical processing, where equipment undergoes frequent washdowns and exposure to sanitizing agents. By providing a robust barrier against contaminants and harsh environments, these interlocks support companies in upholding stringent safety and hygiene standards, preventing accidents and contamination in sensitive applications.
Applications of Stainless Steel Mechanical Interlock Switches
Stainless steel mechanical interlock switches are widely used across industries that demand high durability and resilience, particularly:
- Food and Beverage Processing: Ensuring safe and hygienic access control in areas exposed to water, steam, and cleaning chemicals.
- Pharmaceutical Manufacturing: Maintaining contamination-free environments by withstanding regular sanitization and exposure to sterile conditions.
- Chemical Processing: Withstanding corrosive substances while providing reliable access control to protect workers from hazardous materials.
- Marine and Offshore Applications: Resisting saltwater and extreme environmental conditions that could corrode other materials.
- Heavy-Duty Industrial Settings: Offering high-strength performance in applications involving abrasive materials, intense loads, or high-heat areas.
Conclusion
Investing in proper machine guarding solutions is not just about compliance—it’s about protecting workers, reducing downtime, and ensuring seamless operations. Workplace injuries caused by unguarded machinery can lead to costly disruptions, legal complications, and a loss of productivity. By implementing fixed barriers like concertina guards, businesses can effectively shield operators from moving parts while maintaining accessibility for maintenance.
For applications requiring controlled access, mechanical interlocks offer a secure way to keep gates and doors locked during machine operation. These interlocks work seamlessly with advanced safety switches to ensure that hazardous areas remain inaccessible until it is safe to enter. The use of RFID-coded safety switches further enhances security by requiring specific authorization before access is granted.
Beyond compliance, adopting these machine guarding solutions demonstrates a commitment to workplace safety and operational excellence. Taking proactive steps to install effective safety measures reduces risks, increases employee confidence, and contributes to a more productive and legally compliant work environment. Whether it’s fixed guarding, interlocked access points, or intelligent safety sensors, making the switch to reliable machine guarding is a smart, long-term investment. Start today and build a safer, more efficient industrial workspace.