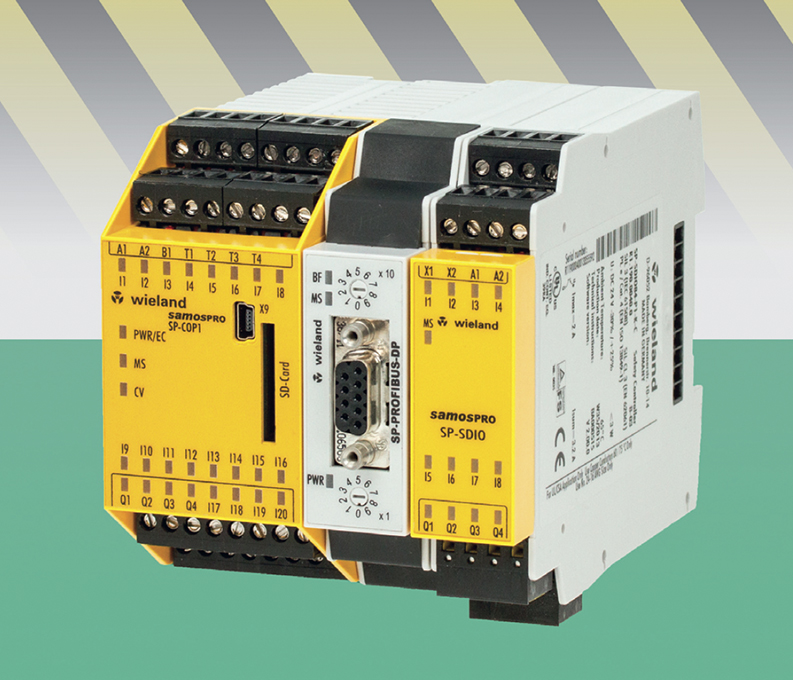
26
What is a Safety PLC
Introduction to Safety PLCs
Safety PLC: Ensuring Functional Safety in Industrial Automation
A Safety PLC is a specialized Programmable Logic Controller designed to ensure functional safety in industrial automation. Unlike standard PLCs, Safety PLCs include fail-safe mechanisms to prevent hazardous failures and protect both operators and equipment.
Engineered to comply with IEC 61508 and ISO 13849, these controllers monitor and control safety-critical processes in real-time, such as emergency stops, machine guarding sensors, switches & interlocks, and fire detection. They enhance safety by:
- Detecting faults before they lead to failures.
- Implementing redundancy and fail-safe functions to maintain system integrity.
- Enabling safe shutdowns in hazardous situations.
Widely used in manufacturing and automated assembly lines, Safety PLCs integrate seamlessly with standard PLCs, ensuring regulatory compliance, operational efficiency, and flexible safety solutions without compromising productivity.
Historical Evolution of PLCs in Industrial Automation
The invention of Programmable Logic Controllers (PLCs) revolutionized industrial automation and the method of controlling machines and processes. Before the PLC, manufacturing systems relied on hardwired relay-based control panels that were complex, inflexible, and difficult to modify.
The introduction of PLCs in the late 1960s was a major breakthrough. Initially designed to replace relay logic in the manufacturing of vehicles, early PLCs provided an easily programmable alternative with less complexity and greater system reliability. As PLC technology spread across industries, advancements in microprocessor technology, communication protocols, and computer software further enabled controllers to be more powerful and versatile.
By the 1990s, industrial automation faced growing demands for greater worker safety and machine reliability, leading to the development of Safety PLCs. Unlike standard PLCs, Safety PLCs were designed with intrinsic redundancy, fault detection, and fail-safe provisions to meet stringent safety standards. Their introduction allowed industries to implement programmable safety functions that could be modified to adapt to evolving operational needs while complying with regulations like IEC 61508 and ISO 13849.
Today, Safety PLCs are an essential component of modern industrial systems, offering real-time monitoring, automated risk mitigation, and seamless integration with traditional automation processes. Their evolution continues with the integration of cybersecurity features, predictive diagnostics, and IoT connectivity, ensuring a safer and smarter industrial future.
Standard PLCs vs. Safety PLCs
Key Differences in Design and Functionality
While both Standard PLCs and Safety PLCs are used for industrial automation, their design and functionality differ significantly based on their intended purpose. A Standard PLC focuses on optimizing efficiency, productivity, and automation control, while a Safety PLC is specifically designed to ensure fail-safe operation and compliance with safety regulations.
Design Differences
- Redundancy & Self-Checking: Safety PLCs feature dual-channel architecture for continuous self-monitoring, unlike single-unit standard PLCs.
- Certified Components: Safety PLCs comply with IEC 61508 and ISO 13849, ensuring reliability in hazardous environments.
- Real-Time Diagnostics: Built-in error detection prevents failures before they escalate.
Functional Differences
- Fail-Safe Operation: Safety PLCs default to a safe state during faults, whereas standard PLCs may continue operating.
- Dedicated Safety Functions: Safety PLCs manage emergency stops, interlocks, and fire detection.
- Strict Programming Standards: Requires certified safety engineers for implementation and validation.
With industries prioritizing worker safety and regulatory compliance, Safety PLCs are essential in high-risk sectors like manufacturing, energy, and transportation. Their integration with automation systems ensures maximum protection and reliability.
A Brief Discussion of Safety InputsÂ
The effectiveness of any safety system, even with a high-quality safety PLC, is highly dependent on its’ ability to detect hazards and trigger appropriate protective responses. As such, safety input products form the foundation of a reliable safety architecture. Selecting the correct components to match specific hazards is essential for maintaining workplace safety.
Venus Automation offers a wide range of safety input devices to suit varied industrial applications. Detection solutions include the safety light curtain range, available for body protection, hand protection, and finger protection. Options supporting long range sensing and outdoor environments are available, along with muting light curtain models designed for automated processes. Supporting components such as photo cells, connection boxes, and muting accessories are also supplied. Additional detection options include multi beam systems and advanced laser scanner technologies.
To detect presence or motion at close range, proximity sensors are available, including non-contact switches, with magnetic or RFID coding technologies. Enclosures come in plastic, metal, or stainless steel variants for application-specific durability.
Mechanical safety detection is supported by products such as safety edge and mounting systems, contact mats, and bumpers with relevant edge accessories., including cabling to transmit signals from these devices. These are ideal for perimeter and surface-triggered protection zones. For advanced zone control, trapped key systems and blocking devices ensure process integrity.
Manual control inputs are also critical in many safety scenarios. Venus Automation provides safety enabling switches, limit switch options, foot pedal switches, control pads, and standard control components.
Together, these input systems interface with the machine’s transmission system, ensuring rapid response to unsafe conditions. Combined with suitable outputs and logic control, they serve as the first line of defence in safeguarding personnel and equipment.
Our Product Range:
Â
Introduction to Wieland Samos PRO Safety PLC Products
A Smart Solution for Industrial Safety
With the rapidly changing industrial scenario in today’s times, ensuring functional safety without compromising productivity is of utmost importance. Wieland Samos PRO Safety PLCs are a high-tech solution for automation of safety by machines, bringing sophisticated programmability, flexibility, and reliability to meet stringent safety requirements.
What Makes Wieland Samos PRO Safety PLCs Unique?
Designed for hostile environments and challenging automation needs, Wieland Samos PRO controllers integrate modular expandability, real-time diagnostics, and high-speed processing to deliver unparalleled safety performance. These space-saving controllers support a wide range of safety-related applications, including emergency stops, light curtains, door interlocks, and motion control safety.
Major Features and Advantages
- Modular and Expandable Design – Flexible enough to be easily customized for small to large-scale applications, with provision for multiple I/O expansions for added flexibility.
- High-Speed Processing – Offers rapid fault detection and immediate safety function execution, reducing downtime hazards.
- Certified Safety Compliance – Fully conforms to IEC 61508, ISO 13849, and EN 62061, ensuring global regulatory compliance.
- User-Friendly Programming – Features samos® PLAN 6 software, offering a simple-to-use, drag-and-drop interface for easy configuration and troubleshooting.
- Reliable Redundancy & Self-Monitoring – Dual-channel architecture with built-in diagnostics ensures fail-safe operation in harsh safety applications.
Versatility Across Industries
Wieland Samos PRO Safety PLCs are widely used in manufacturing, robotics, logistics, and heavy industry, where accuracy, speed, and safety integration are top priorities. Their seamless compatibility with fieldbus systems like PROFIBUS, CANopen, and EtherCAT makes them ideal for Industry 4.0 applications.
By leveraging the functionality of Wieland Samos PRO, companies can achieve high safety levels, greater efficiency, and reduced operational risks, making them an essential choice for modern automated safety systems.
Ensure maximum safety in your automation system with the Wieland Samos PRO Safety PLC, designed for flexible and reliable machine control.
Wieland samos SP-COP2-ENI-A Safety Controller
Model: R1.190.1310.0
Wieland samos SP-COP2-EN-P-A Safety Controller
Model: R1.190.1230.0
Wieland samos SP-COP2-EN-IO-A Safety Controller
Model: R1.190.1220.0
Wieland samos SP-COP2-EN-A Safety Controller
Model: R1.190.1210.0
Introduction to Pizzato GEMNIS Safety PLC
Innovative Safety Control for Modern Automation
As industrial automation becomes more sophisticated, the need for intelligent, powerful, and flexible safety solutions has never been more pressing. Pizzato GEMNIS Safety PLC is an advanced programmable safety controller that simplifies safety management, enhances efficiency, and ensures compliance with the latest safety regulations. Designed for flexibility and scalability, GEMNIS PLCs provide industries with a robust solution for protecting people and machines.
Why Choose Pizzato GEMNIS Safety PLC?
Pizzato’s GEMNIS series stands out with its modular design, real-time diagnostics, and compatibility with automation systems. Suitable for high-risk industrial environments, these controllers efficiently handle emergency stop functions, access control, motion safety, and process monitoring while meeting the highest safety standards.
Key Features and Benefits
- Modular & Expandable Configuration – Adaptable for small to large-scale applications, offering flexibility for customized safety configurations with expandable I/O modules.
- Advanced Diagnostics & Monitoring – Predictive maintenance and real-time fault detection help eliminate unexpected failures.
- Certified Safety Compliance – Meets all requirements of ISO 13849-1, IEC 62061, and IEC 61508, ensuring fail-safe operation in critical applications.
Applications Across Industries
The Pizzato GEMNIS Safety PLC is widely used in manufacturing, robotics, material handling, and packaging industries, where precision and safety are essential. Its compatibility with existing automation infrastructure makes it a preferred choice for Industry 4.0 installations, ensuring both performance and regulatory compliance.
With its sophisticated technology and high safety functionality, Pizzato GEMNIS Safety PLC helps industries achieve enhanced safety, operational efficiency, and seamless automation, making it a trusted choice for modern industrial safety solutions.
Optimize your industrial automation with the Pizzato GEMNIS Safety PLC, offering advanced safety and control solutions.
Pizzato CS MF202M0-P3 Safety Module
Model: SIL 3, PL e, IP20
Pizzato CS MF202M0-P4 Safety Module
Model: SIL 3, PL e, IP20
Pizzato CS MF202M0-P5 Safety Module
Model: SIL 3, PL e, IP20
Pizzato CS MF202M0-P6 Safety Module
Model: SIL 3, PL e, IP20
Introduction to ReeR MOSAIC Safety PLC
A Scalable and Intelligent Safety Solution
With increasing industrial automation, there is always greater demand for flexible and reliable safety control systems. ReeR MOSAIC Safety PLC is a highly advanced, modular safety controller that attempts to simplify machine safety management to the extreme extent while being within international standards for safety. It provides an expandable, low-cost, and user-friendly solution for applications in industries demanding integrated safety on several applications.
Why Select ReeR MOSAIC Safety PLC?
ReeR MOSAIC is unique in its ability to minimize wiring, simple programming, and enhanced safety diagnostic capabilities. In contrast to traditional safety relays, MOSAIC offers an integrated solution where safety devices such as emergency stops, light curtains, interlocks, and two-hand control systems can be easily integrated.
Key Features and Benefits
- Modular and Expandable Design – Expandable with different I/O modules, thus suitable for small as well as big industrial safety applications.
- Simplified Installation and Wiring – Simplifies the complexity of traditional relay-based safety systems, hence incurring less cost and easy installation.
- Safety Compliance Certified – Fully meets IEC 61508, ISO 13849-1, and IEC 62061 standards, hence conforming to the highest functional safety standards.
- User-Friendly Configuration – Simple drag-and-drop programming with MOSAIC Safety Designer software, hence easy to configure safety logic.
- Real-Time Monitoring and Diagnostics – Provides real-time feedback and remote monitoring capabilities, guaranteeing constant operational safety.
Versatility Across Industries
The ReeR MOSAIC Safety PLC is highly versatile across industries, used in manufacturing, robotics, logistics, and process automation, where precision and compliance with safety standards are crucial. Its degree of integration with fieldbus protocols like PROFIBUS, CANopen, and EtherNet/IP makes it a suitable answer for Industry 4.0 applications.
By virtue of its module-based structure, advanced diagnostics, and simple installation, ReeR MOSAIC Safety PLC allows industries to achieve higher safety levels, higher efficiency, and advanced machine control, making it a trusted option for modern industrial automation.
Enhance your safety system with the ReeR MOSAIC Safety PLC, a modular and configurable solution for machine safety applications.
ReeR MOSAIC – MA2
Analog Input Expansion Unit for M1 – 1100026
ReeR MOSAIC – MA2C
Analog Input Expansion Unit for M1 – 1100126
ReeR MOSAIC – MA4
Analog Input Expansion Unit for M1 – 1100025
ReeR MOSAIC – MI12T8
Expansion Units for M1 Safety PLCs – 1100022
Machine Guarding and Safety PLCs
Optimizing Safety with Intelligent Machine Guarding
Machine tools are the leading cause of hazards, and hence preventive safety measures are of utmost importance. While traditional safety barriers, electronic key systems and mechanical interlocks provide basic protection, they are insensitive to dynamic conditions. Safety PLCs enhance machine guarding by incorporating real-time monitoring, automated hazard watch, and smart control, assuring worker safety and process perfection.
How Safety PLCs Strengthen Machine Guarding
In contrast to conventional safety systems, Safety PLCs can integrate intelligent sensors, lockout automation, and controlled gates. They continuously check data from safety devices such as light curtains, area scanners, safety mats and two-hand control systems, and ensure the machines operate in safe states only. With dynamic control capabilities, they process multiple zones of safety in parallel, reducing unnecessary shutdowns while maintaining very high levels of protection.
One of the strongest benefits of Safety PLCs is that they recognize dangerous conditions and halt operations instantly before an accident occurs. They adjust safety parameters according to changing operating conditions, allowing greater production flexibility in planning. Unlike traditional relays requiring full system shutdowns, Safety PLCs support selective stopping, which saves downtime and increases continuity of workflow. They are also easily compatible with existing industrial control networks, supporting predictive diagnostics and remote monitoring to further optimize overall efficiency.
Where Safety PLCs Bring Value
Wherever assembly lines and conveyor belts, robotic stations, and beyond, Safety PLCs are redefining machine guarding in manufacturing, packaging, logistics, and automotive production industries. By linking safety with productivity, they help businesses maintain unbroken operations while ensuring the welfare of workers. Beyond fixed traditional safety settings, Safety PLCs offer adaptive intelligent protection that senses and adjusts to changing production landscapes.
The Evolving Role in Industry 4.0
With advancements in industry automation, Industry 4.0 is revolutionizing the manner in which humans, systems, and machines communicate. Safety Programmable Logic Controllers (PLCs) are no longer just reactive safety devices; they are now part of intelligent automation, which enables direct machine-to-machine communication and centralized control networks.
Modern Safety PLCs are also capable of interfacing with IoT-enabled devices, cloud computing, and predictive maintenance technologies, with real-time monitoring and adaptive safety reaction. Their ability to process massive amounts of data allows for faster decision-making, self-diagnosis, and remote access, promoting productivity and workplace safety.
As smart factories take root, Safety PLCs are helping industries transition towards more networked and automated production lines. Their capability to keep up with evolving safety regulations as well as enhance efficiency and flexibility in operations makes them a central element of Industry 4.0, which is a bridge between automation, safety, and digitalization.